In the world of machinery and engineering, few components are as quietly essential as the humble gasket. Whether it’s keeping oil inside an engine or ensuring a waterproof seal on an electronic device, the design of gasket can make or break a system’s performance. But what exactly goes into creating one? This article takes a deep dive into what are gaskets, how they function, the materials they’re made from, and the practical steps to craft a custom gasket solution—offering a clear path for anyone looking to master this critical skill.
What Are Gaskets?
To kick things off, let’s answer the basics: what are gaskets? Simply put, a gasket is a mechanical seal that fills the space between two mating surfaces, preventing leaks of fluids or gases. You’ll find them everywhere—from car engines to kitchen appliances—quietly doing their job.
How Do Gaskets Work?
At its core, gasket design is about creating a barrier that seals two mating surfaces. Gaskets work by filling microscopic irregularities—gaps as small as 0.01 mm—between these surfaces, preventing the escape of fluids or gases under pressure. When compressed (typically between 0.1 and 10 MPa), the gasket deforms to conform to imperfections, distributing stress evenly to maintain a tight seal.
The sealing mechanism varies by application:
- Static Sealing: In scenarios like flange joints or pipe fittings, gaskets rely on material flexibility to maintain a fixed seal under constant pressure.
- Dynamic Sealing: In moving systems like pumps or engines, gaskets must resist wear and retain elasticity to accommodate vibration or thermal expansion.
This adaptability is why gasket design is both a science and an art, requiring precise engineering to match the gasket’s properties to its working environment.
Common Gasket Types
Not all gaskets are cut from the same cloth—gasket types vary to tackle different challenges. Here’s a rundown of the big players:
- Flat Gaskets: Simple sheets cut into shapes like rings or rectangles—think oil pan seals. They’re cheap and versatile, often rubber or composite.

- O-Rings: Round and doughnut-like, these fit into grooves for a snug seal—great for hydraulic systems or water pipes.
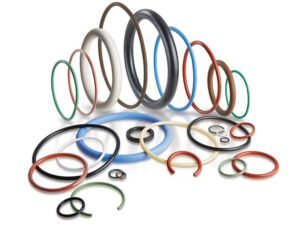
- Spiral Wound Gaskets: Metal strips wound with filler (like graphite), built for high heat and pressure—think industrial boilers at 500°C.

- Form-in-Place (FIP) Gaskets: Liquid material cures right on the surface—no cutting needed. Perfect for weird shapes in electronics.

- Metal Jacket Gaskets: Soft cores wrapped in metal, blending flexibility with toughness for engines or turbines.
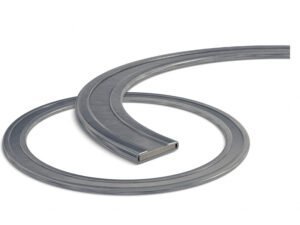
Each type shapes the design of gasket, matching the job—whether it’s soaking up oil or shrugging off steam.
Application Examples
Custom gasket design shines across industries:
- Automotive: Nitrile rubber gaskets seal engine oil pans, enduring 120°C and 5 MPa pressure.
- Electronics: Silicone gaskets in outdoor devices achieve IP67 waterproofing, resisting -20°C to 80°C cycles.
- Medical: Polyurethane foam gaskets in ventilators provide soft, durable seals for patient safety.
These cases illustrate how tailored gasket design meets diverse performance demands.
Key Considerations for Custom Gasket Design
Gaskets are critical components in mechanical systems, ensuring reliable sealing to prevent leaks of liquids, gases, or particulates. Beyond sealing, gaskets may also provide insulation, vibration dampening, or electromagnetic interference (EMI) shielding. Designing the right gasket requires a systematic approach that balances performance, cost, and manufacturability.
1. Functional Requirements
The first step in gasket design is understanding its purpose and application. Key questions include:
- Sealing Objective: Will the gasket prevent leaks of water, oil, gas, or chemicals? Does it need to block dust, noise, or EMI?
- Static vs. Dynamic: Is the gasket for a stationary joint (e.g., flange) or a moving part (e.g., rotating shaft)? Dynamic applications demand higher elasticity and wear resistance.
- Service Life: Is the gasket for one-time use (e.g., maintenance) or long-term durability (e.g., industrial pipelines)?
For example, a gasket for food processing equipment must meet FDA standards for non-toxicity, while one for aerospace may require EMI shielding. Clearly defining these requirements sets the foundation for material and design choices.
2. Select the Appropriate Material
Material selection is pivotal, as it determines the gasket’s performance under specific conditions. Key factors include:
- Chemical Compatibility: The material must resist degradation from contact with media like acids, oils, or solvents. Common options include:
- Nitrile Rubber: Ideal for oily environments.
- Viton (Fluorocarbon): Suited for harsh chemicals and high temperatures.
- PTFE: Chemically inert for corrosive media.
- Graphite: Excellent for high-temperature, high-pressure applications.
- Temperature Range: The material must withstand the minimum and maximum operating temperatures. Silicone performs well from -50°C to 200°C, while metal gaskets suit extreme heat (>500°C).
- Compression and Recovery: The material should compress to fill surface gaps while maintaining resilience to avoid permanent deformation. Low compression set materials like premium silicone are ideal for long-term sealing.
- Environmental Resistance: Consider exposure to UV, ozone, humidity, or salt spray. EPDM excels in outdoor applications due to its weather resistance.
4. Design Geometry and Dimensions
The shape and size of a gasket play a big role in how well it seals and how easy it is to install. It’s important to match the gasket’s shape to the sealing surface—whether it’s round, square, or something more customized. For complex designs, processes like waterjet or laser cutting might be needed. Thickness matters too: rougher surfaces need thicker gaskets, usually around 3–6 mm, to fill in any uneven spots, while smoother surfaces can use thinner gaskets—1–2 mm is often enough and helps cut costs. The type of gasket cross-section also makes a difference. Flat gaskets and O-rings are common, but for high-pressure and high-temperature applications, spiral-wound gaskets are often the better choice. And no matter the type, getting the size just right is key—if it’s too loose, it may leak; too tight, and it can be tough to install.
5. Account for Operating Conditions
The gasket must perform reliably under real-world conditions:
- Pressure and Temperature: Match the gasket to the system’s pressure (low: <100 psi; high: >1000 psi) and temperature fluctuations. Thermal expansion or contraction can loosen seals, requiring materials with low compression set.
- Surface Characteristics: Flange roughness, flatness, or defects influence gasket choice. Rough surfaces need softer, thicker materials; smooth surfaces allow harder, thinner gaskets.
- Dynamic Factors: Vibration, shock, or thermal cycling demand high resilience and fatigue resistance.
- External Environment: UV, humidity, salt spray, or EMI may degrade performance. For instance, outdoor equipment needs UV-resistant EPDM, while electronics may require conductive gaskets.
6. Optimize for Manufacturing and Assembly
A practical gasket design also needs to consider how it will be made and installed. Common processes include die-cutting for simple shapes in large quantities, waterjet cutting for complex or low-volume parts, and injection molding for high-precision or 3D gaskets. For prototypes, flexible methods work well, while molds help reduce cost in mass production. Adding features like adhesive backing, alignment holes, or pull-tabs can make installation easier and help avoid mistakes.
7. Ensure Regulatory Compliance
Gaskets have to follow different rules depending on where they’re used. For example, food-grade gaskets must be safe for food, and ones used in pipes or airplanes need to meet special safety standards. Some places also require the materials to be fire-safe or low in smoke. And nowadays, it’s important to avoid harmful stuff like asbestos and try to use materials that can be recycled.
Conclusion
Effective gasket design is the backbone of reliable sealing systems, blending an understanding of how gaskets work with smart material choices and precise customization. By addressing application-specific needs, optimizing shape and thickness, and validating through testing, custom gaskets can solve even the toughest sealing challenges. Whether you’re designing for an engine, an electronic device, or a medical tool, mastering gasket design unlocks efficiency and longevity—making it a critical skill for any manufacturer.
Flexiparts as a professional on-demand manufacturer, whether prototype or mass production, , offering precision gasket design and production services.