Injection molding material selection plays a crucial role in determining the performance, durability, and functionality of the final product. The right molding materials ensure precision, strength, and cost-effectiveness while catering to industry-specific needs. From automotive components to consumer electronics, selecting the ideal injection molding materials directly influences product longevity and production efficiency.
Understanding what material is used in injection molding requires a detailed exploration of different material classifications, each with unique mechanical properties and processing characteristics. The primary categories of molding materials include thermoplastics, thermosets, and elastomers—each offering distinct advantages based on the application’s requirements.
Classification of Injection Molding Materials
Material selection in injection moulding materials is broadly categorized based on their behavior during heating and cooling cycles. The three major types are thermoplastics, thermosets, and elastomers, each suited for different applications.
Thermoplastics
Thermoplastics are the most commonly used injection molding materials, primarily due to their ability to be melted, molded, and re-melted multiple times without significant degradation. This makes them ideal for high-volume manufacturing with minimal material wastage. Some key characteristics include:
- Excellent impact resistance and toughness
- Recyclability, making them environmentally friendly
- Versatility in color, texture, and transparency
- Resistance to moisture, chemicals, and UV exposure
Common thermoplastic materials used in injection molding include:
- Acrylonitrile Butadiene Styrene (ABS): Known for its toughness and dimensional stability, widely used in automotive and consumer goods.
- Polypropylene (PP): Offers high chemical resistance and flexibility, commonly used in medical and food-grade applications.
- Polycarbonate (PC): Transparent and impact-resistant, suitable for safety equipment and electronic casings.
- Polyethylene (PE): Available in low and high-density variations, widely used in packaging and industrial applications.
Thermosets
Unlike thermoplastics, thermoset molding materials undergo an irreversible curing process. Once molded, these materials cannot be re-melted, making them ideal for high-heat and structurally rigid applications.
Key attributes of thermosetting injection molding materials include:
- High thermal stability and resistance to deformation
- Exceptional chemical and electrical insulation properties
- Superior strength and rigidity
Common thermosetting materials used in injection molding:
- Epoxy Resins: Frequently used in aerospace and automotive industries for high-strength applications.
- Phenolic Resins: Excellent heat and chemical resistance, often found in electrical components.
- Melamine & Urea Formaldehyde: Common in kitchenware and electrical casings due to their hardness and surface finish.
Elastomers
Elastomers, also referred to as rubber-like materials, possess high elasticity and flexibility, making them suitable for applications requiring resilience and impact absorption. These materials combine the characteristics of both thermoplastics and thermosets, offering durability and shock resistance.
Key properties of elastomeric injection molding materials:
- High elongation and flexibility
- Excellent resistance to wear and fatigue
- Good weather and chemical resistance
Examples of elastomers used in injection molding:
- Thermoplastic Elastomers (TPE): Blend of rubber and plastic, used in soft-touch grips and seals.
- Silicone Rubber: High heat resistance, commonly found in medical and food-grade products.
- Polyurethane (PU): Offers toughness and abrasion resistance, ideal for wheels and industrial parts.
Understanding these material classifications provides a foundation for selecting the best injection molding material based on performance, production efficiency, and end-use application.
Common Types of Thermoplastic Materials Used in Injection Molding
Thermoplastics are the dominant injection molding materials due to their ability to be reshaped and recycled without significant degradation. They offer a balance of strength, durability, and processing ease, making them ideal for diverse applications. Below are some of the most widely used thermoplastic molding materials, each with unique properties suited for different industries and injection molding service.
Acrylonitrile Butadiene Styrene (ABS) – Strength, Durability, and Versatility
ABS is a widely used injection molding material known for its toughness, impact resistance, and excellent machinability. It is a blend of acrylonitrile, butadiene, and styrene, each contributing to its durability, flexibility, and smooth surface finish.
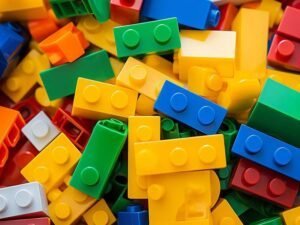
Key benefits of ABS:
- High impact resistance and toughness
- Good dimensional stability
- Easy to mold and post-process (painting, plating, or bonding)
Applications: Automotive components, consumer electronics, and household appliances.
Nylon (Polyamide, PA) – Wear Resistance and High Performance
Nylon is a high-performance moulding material valued for its wear resistance, low friction, and chemical stability. It is commonly reinforced with glass fibers to enhance its mechanical properties.
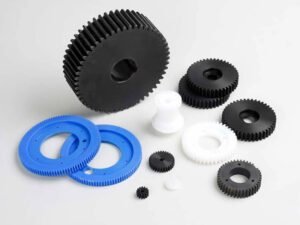
Key benefits of Nylon (PA):
- High tensile strength and abrasion resistance
- Excellent thermal and chemical resistance
- Low friction, making it ideal for moving parts
Applications: Gears, bearings, automotive fuel systems, and industrial components.
Polycarbonate (PC) – Optical Clarity and Impact Resistance
Polycarbonate is a transparent and highly durable injection material often used as an alternative to glass. It provides superior impact resistance while maintaining optical clarity.

Key benefits of PC:
- High strength and shatter resistance
- Excellent light transmission (up to 90%)
- Heat and flame resistance
Applications: Eyewear lenses, medical devices, protective gear, and electronic enclosures.
Polyethylene (PE) – HDPE vs. LDPE and Their Applications
Polyethylene is one of the most commonly used injection moulding materials, available in different densities: high-density polyethylene (HDPE) and low-density polyethylene (LDPE).
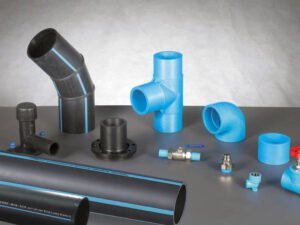
- HDPE: Higher strength, chemical resistance, and rigidity
- LDPE: More flexible, lightweight, and impact-resistant
Applications: Containers, packaging, pipes, and industrial storage tanks.
Polypropylene (PP) – Chemical Stability and Flexibility
Polypropylene is a lightweight, flexible, and chemically resistant molding material widely used in medical, automotive, and packaging industries.
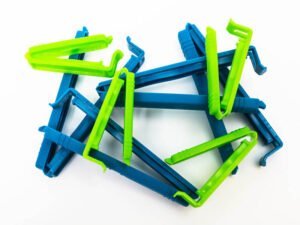
Key benefits of PP:
- High chemical and moisture resistance
- Excellent fatigue resistance (hinges and snap-fit parts)
- Low density, reducing part weight
Applications: Medical syringes, food containers, automotive components, and living hinges.
Polystyrene (PS) – Rigid, Cost-Effective, and Easy to Mold
Polystyrene is a low-cost injection molding material that offers ease of processing, rigidity, and good dimensional stability.

Key benefits of PS:
- Lightweight and easy to mold
- Good electrical insulation properties
- Available in high-impact (HIPS) and general-purpose (GPPS) variants
Applications: Disposable cutlery, CD cases, medical packaging, and insulation panels.
Thermoplastic Elastomers (TPE) – Rubber-Like Flexibility with Plastic Processing Benefits
TPE combines the flexibility of rubber with the processing advantages of thermoplastics. It can be molded, extruded, and recycled, unlike traditional rubber.

Key benefits of TPE:
- Soft-touch, flexible, and stretchable properties
- Good resistance to weathering and chemicals
- Can be co-molded with rigid plastics for enhanced grip
Applications: Grips, seals, automotive parts, and medical tubing.
Polyoxymethylene (POM) – Precision Engineering and Low-Friction Applications
POM, commonly known as acetal or Delrin, is a high-strength injection moulding material with excellent wear resistance and dimensional stability.
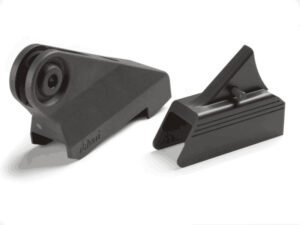
Key benefits of POM:
- Low friction and excellent mechanical properties
- High rigidity and fatigue resistance
- Good chemical resistance to solvents and fuels
Applications: Gears, automotive fuel systems, conveyor belts, and electrical components.
Acrylic (PMMA) – Optical Transparency and UV Resistance
Acrylic, also known as PMMA, is a transparent plastic that serves as an alternative to glass. It offers excellent UV resistance and optical clarity.
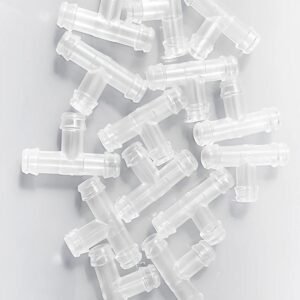
Key benefits of PMMA:
- Excellent light transmission (92%)
- High surface hardness and scratch resistance
- Resistant to weathering and aging
Applications: Display screens, lenses, signage, and aquariums.
Polyethylene Terephthalate (PET) – Recyclability and Strength
PET is a widely used injection molding material known for its recyclability and high tensile strength. It is commonly used in packaging and textile industries.

Key benefits of PET:
- High strength and impact resistance
- Excellent barrier properties for moisture and gases
- 100% recyclable, making it eco-friendly
Applications: Beverage bottles, food packaging, and textile fibers.
Choosing the right molding materials depends on the application, cost constraints, and desired mechanical properties. Understanding the properties of these common injection moulding materials ensures better product performance and manufacturing efficiency.
Why Rubber Is Not Commonly Used in Injection Molding
Rubber materials are not as commonly used in traditional injection molding processes as other injection molding materials like thermoplastics. This is primarily due to the material limitations and the inherent challenges of molding rubber. The complexities associated with its molding process and material behavior make rubber less favorable for mass production via injection molding.
Material Limitations and Challenges in Rubber Injection Molding
Rubber, particularly natural rubber and most synthetic rubbers, has unique properties that make it challenging to process in traditional moulding systems.
- Viscosity: Rubber materials generally have a higher viscosity compared to typical injection molding materials. This makes it more difficult to inject into molds, especially under high-pressure conditions required for injection molding.
- Flow characteristics: Rubber does not flow as easily as thermoplastics, which means it can be difficult to fill the mold completely and uniformly without experiencing defects like voids or incomplete parts. This impacts both the quality of the finished product and the efficiency of the molding process.
- Curing requirements: Most rubber materials require a curing process, such as vulcanization, to achieve the desired physical properties (e.g., elasticity, strength). In traditional injection molding, the curing step typically occurs in a separate process known as compression molding or transfer molding. This adds complexity and time to the production cycle, making rubber less suited for high-volume injection molding.
- Shrinkage and deformation: Rubber materials tend to shrink or distort during cooling, which can affect the final dimensions of the molded parts. This can lead to challenges in ensuring dimensional accuracy and consistency when producing complex or detailed parts.
Injection Molding Process Constraints for Rubber Materials
The constraints of the injection molding process itself further contribute to the challenges of using rubber materials. The standard injection molding machines are designed primarily for thermoplastic processing, and adapting them to handle rubber requires significant modifications.
- Temperature Control: Rubber needs specific temperature control to ensure proper molding and curing. However, traditional injection molding machines are optimized for thermoplastics, where material flows freely at higher temperatures. The low flowability of rubber, combined with its need for a specific curing temperature range, adds complexity to the process.
- Mold Design: Designing molds for rubber materials often requires specialized features like precise venting and cooling channels to control the curing and cooling rates. This is different from designing molds for thermoplastics, where such considerations are less critical. The need for these additional features further drives up tooling costs and manufacturing time.
- Cycle Time: The injection molding cycle for rubber tends to be longer than for thermoplastics because of the additional curing time required. This increase in cycle time directly impacts production rates, which can be a disadvantage in high-volume applications.
Alternative Materials: TPEs, Liquid Silicone Rubber, and Other Substitutes
Due to these challenges, manufacturers often turn to alternative materials that can offer the same flexibility, elasticity, and durability as rubber, but with improved compatibility for the injection molding process.
- Thermoplastic Elastomers (TPEs): TPEs are a popular alternative to traditional rubber in injection molding. These materials combine the characteristics of rubber with the easy processing advantages of thermoplastics. TPEs have a lower viscosity and flow more easily during molding, making them ideal for injection molding applications. They also offer excellent flexibility and are highly resistant to wear, weathering, and aging.
- Liquid Silicone Rubber (LSR): LSR is a highly flexible and durable material that can be used in injection molding. Unlike solid rubbers, LSR is injected in a liquid form and then cured during the molding process. It offers excellent elastic properties, high-temperature resistance, and biocompatibility, making it ideal for medical, automotive, and consumer product applications.
Key Factors in Selecting Injection Molding Materials
Mechanical Properties
- Strength and Durability: Consider the tensile strength, flexural modulus, and impact resistance required for the product’s intended use.
- Flexibility vs. Rigidity: Choose materials that balance flexibility and rigidity based on the application.
Thermal Properties
- Heat Resistance: Ensure the material can withstand the operating temperature range without degrading.
- Thermal Stability: Consider how the material maintains its shape and properties under varying temperatures.
Chemical Properties
- Chemical Resistance: Select materials that resist chemicals and moisture to prevent degradation.
- Oxidation Resistance: Important for materials exposed to air or chemicals that could cause oxidation.
Aesthetic and Finish Requirements
- Color and Transparency: Decide on the desired color and transparency of the final product.
- Surface Finish: Consider any post-processing treatments like painting or plating.
Regulatory and Compliance Needs
- Industry-Specific Regulations: Ensure compliance with regulations such as FDA for medical devices or RoHS for electronics.
- Safety Standards: Verify that the material meets relevant safety standards.
Cost and Availability
- Material Cost: Evaluate the cost of the material relative to the project budget.
- Processing Costs: Consider the cost of processing, including cycle times and scrap rates.
Moldability and Processability
- Flow Characteristics: Ensure the material flows well during molding to minimize defects.
- Shrinkage Rates: Consider how the material shrinks during cooling to maintain dimensional accuracy.
Conclusion
Choosing the right injection molding material is essential for ensuring product quality, durability, and cost-effectiveness. With options ranging from thermoplastics like ABS, PC, and PP to specialized materials like TPE and POM, each offers unique benefits for different applications. Factors such as mechanical strength, thermal resistance, chemical compatibility, and production efficiency must be carefully considered. By optimizing material selection, manufacturers can enhance performance, reduce defects, and improve overall production efficiency, paving the way for innovation and sustainability in injection molding applications.