Injection moulding medical products is at the heart of modern healthcare manufacturing, providing the precision and reliability needed for critical medical devices. This versatile process enables the production of everything from syringes and implants to diagnostic tools and prosthetics, ensuring both safety and performance in every component. In this article, we explore the role of injection moulding in the medical industry, the processes and materials involved, its numerous benefits, and the wide range of applications it supports. Whether you’re involved in designing medical devices or seeking innovative manufacturing solutions, understanding the power of injection moulding is key to advancing medical technology.
The Role of Injection Molding in the Medical Industry
Injection molding is crucial in the medical industry, enabling the production of high-quality components that meet strict safety standards. Known for its precision, cost-efficiency, and scalability, it produces everything from small parts to large devices. This versatile method ensures consistent quality, reliability, and biocompatibility, making it ideal for disposable products and complex surgical tools used in sensitive medical environments.
Medical Injection Molding Process
Medical injection molding is a specialized manufacturing process vital to the healthcare industry for producing precise, high-quality, and sterile medical devices and components. It involves injecting molten medical-grade polymers into a mold cavity under high pressure. This technique is capable of mass-producing parts with intricate geometries while adhering to strict regulatory standards, such as FDA guidelines and ISO certifications. Medical injection molding is used in creating a wide array of medical products, including implants, surgical instruments, drug delivery systems, syringes, IV components, and diagnostic equipment.
Several types of injection molding processes are used in the medical field:
Conventional Injection
Molding This widely used process involves injecting molten plastic into a mold cavity under high pressure and is suitable for parts like syringes and IV components.
Thin Wall Injection Molding
This specialized process is designed for creating parts with extremely thin walls (under 1mm), which is ideal for lightweight, high-strength components and can lead to cost savings in high-volume production.
2-Shot Molding (Two-Shot Molding)
This technique molds and over-molds a medical device in a single operation, allowing for intricate designs and the combination of different materials to enhance functionality and appearance.
Insert Molding
Similar to overmolding, molding insert service process uses a preformed part that is loaded into a mold and then over-molded with a thermoplastic resin to create the final medical devices components.
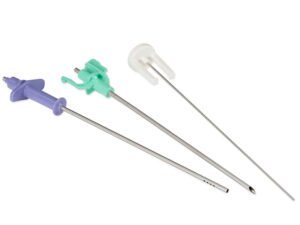
Gas-Assisted Injection Molding
This process involves running gas through channels in the mold to ensure thicker parts dry evenly, preventing misshapen structures and weakness.
Liquid Silicone Injection Molding
Liquid silicone rubber injection molding (LSR) is a method that forces liquid silicone into a mold cavity, where it cures quickly into the final part shape. This process offers efficient production, consistent part quality, and improved productivity.
3D Printing
Although not technically injection molding, 3D printing is used to create prototypes and test designs before injection molding. It can also be used to create the injection molds themselves, using either metal or plastic.
Materials Used in Medical Injection Molding
Materials used in medical injection molding are carefully selected to meet the specific requirements of medical device manufacturing. The materials must be biocompatible, durable, and resistant to degradation when exposed to bodily fluids or harsh sterilization processes.
Polycarbonate, for example, is ideal for products like syringes and diagnostic equipment for its clarity and strength.
Polypropylene is known for its chemical resistance and low moisture absorption, making it suitable for single-use medical devices.
PE material (Polyethylene) is commonly used to produce medical products such as infusion tubes, syringes, medicine bottles, surgical gloves, and disposable items for its corrosion resistance and biocompatibility.
Medical-grade silicone is often used for its flexibility and ability to withstand autoclaving processes.
Additionally, custom compounds and blends of these materials are often developed to meet specific device requirements, ensuring both functionality and safety.
Benefits of Injection Molding in Medical Device Production
Complex Geometries
The benefits of injection molding in the medical device production process are substantial. One of the primary advantages is its precision and ability to produce complex shapes with tight tolerances. This is especially important in the medical industry, where even the smallest deviation in a component can impact the performance of a device and, by extension, patient safety.
Consistency and Repeatability
Another benefit is the ability to mass-produce high-quality components with consistent quality control. Injection molding allows manufacturers to produce thousands or even millions of identical parts, ensuring that every component meets the same high standards of reliability and functionality. This is essential for devices such as catheters, implants, and surgical instruments, where quality consistency is paramount.
Cost-Effectiveness
Cost-efficiency is another significant advantage. Injection molding allows for high-volume production, which reduces the cost per unit. Once the mold is created, the cost to produce additional units decreases, making it ideal for both large and small medical device manufacturers. Additionally, the speed of the process allows for faster time-to-market, enabling manufacturers to meet the demands of the rapidly evolving medical industry.
Applications of Injection Molding in Medical Devices
Injection molding is widely used across various medical applications due to its ability to produce precise, complex, and reliable components. Some of the most common medical products made with injection molding include:
- Syringes and Needles
- Surgical Instruments
- Drug Delivery Devices
- Diagnostic Tools and Equipment
- Implants and Prosthetic
- Catheters
- Packaging for Medical Products
- Dental Devices
Each of these applications demonstrates the versatility and precision that injection molding brings to the medical industry, allowing manufacturers to produce high-quality, reliable, and safe components for various medical devices.
Medical Parts Injection Molding Considerations
Materials Selection
While the benefits of medical injection molding are evident, there are several critical considerations that manufacturers must take into account. First and foremost, material selection plays a vital role in the process. Medical parts must be made from biocompatible materials that do not elicit an adverse reaction when in contact with the body. Additionally, materials must meet specific standards for sterilization and resistance to chemical degradation, especially for devices used in invasive procedures.
Regulatory Compliance
Another important consideration is regulatory compliance. Medical device manufacturers must ensure that their products meet the strict requirements set by regulatory bodies such as the FDA and ISO. This includes ensuring that the injection molding process adheres to quality control standards, that proper documentation is maintained, and that rigorous testing is conducted to ensure the safety and efficacy of the final products.
Cleanroom
Cleanroom environments are also often required in medical injection molding processes to prevent contamination. The risk of contamination is high in the medical field, and the use of cleanroom helps maintain product integrity by minimizing exposure to particulate matter and bacteria.
Conclusion
Injection molding plays a pivotal role in the medical industry, ensuring the production of high-quality, precise, and reliable components for medical devices. From syringes and surgical instruments to diagnostic tools and implants, the versatility of medical injection molding meets the stringent demands of healthcare manufacturing. With its ability to produce complex geometries and ensure consistent quality, injection molding remains an invaluable technology in medical device production.
If you’re looking to enhance your medical product designs with reliable, cost-effective manufacturing solutions, now is the perfect time to explore injection molding. Reach out to Flexiparts and discover how this advanced process can elevate your product development!