Low Cost Injection Molding has become a crucial goal for manufacturers aiming to stay competitive while maintaining high-quality standards. This article explores various strategies to minimize costs in the injection molding process without compromising product integrity. From optimizing mold designs to selecting cost-effective materials and production methods, this guide provides actionable insights on how to reduce expenses across different stages of production. Whether you’re looking to cut down on tooling costs, improve efficiency, or explore alternative molding technologies, the methods outlined here will help you achieve affordable, high-quality results.
Choosing Cost-Effective Plastic Materials
Material selection directly affecting production expenses and product performance in low cost injection molding(such as overmolded solution and molded inserts). Some thermoplastics offer excellent affordability without compromising essential properties.
- Polypropylene (PP): Low density, chemical resistant, and widely used in consumer goods and automotive components.
- Polyethylene (PE): Durable and cost-effective, commonly used in packaging and piping.
- Acrylonitrile Butadiene Styrene (ABS): Offers good impact resistance and surface quality, ideal for electronics and automotive applications.
- Polystyrene (PS): Inexpensive but brittle, mainly used for lightweight, disposable items.
- Polyvinyl Chloride (PVC): Versatile and affordable, suitable for construction and medical components.
Impact on Injection Molding Costs
Material choice influences plastic injection mold cost through processing efficiency, cycle time, and durability. Low-viscosity plastics like PP and PE reduce cycle time and energy usage, making them ideal for cheap injection molding. Conversely, materials with higher processing temperatures demand more energy and tool wear, increasing costs. Strategic selection of thermoplastics ensures both cost savings and quality.
Optimize the Injection Mold Design
Achieving low cost plastic injection molding requires a holistic approach. In plastic injection molding, mold costs can account for 20% to 30% of the total production cost. As a result, optimizing mold design is a key strategy for achieving low cost plastic injection molding.
Implementing Cost-Efficient Mold Designs
In the pursuit of low cost injection molding, optimizing mold design plays a pivotal role. Mold design directly influences both initial fabrication costs and long-term production expenses. A well-thought-out design can drastically reduce material waste, cycle times, and maintenance costs, while simultaneously improving part quality and consistency. Below are some strategies that directly impact mold fabrication costs and overall production efficiency.
Reducing Mold Fabrication Costs
Simplifying mold designs reduces fabrication costs. Avoiding complex features like intricate cavities and undercuts lowers the need for more material, labor, and time. Additionally, using quick-change inserts or removable cores makes adjustments easier, reducing the need for entirely new molds.
Single-Cavity vs. Multi-Cavity Molds

Single-cavity molds are cheaper but less efficient for high-volume production. Multi-cavity molds, while more expensive upfront, allow for the production of multiple parts per cycle, decreasing the cost per part. For high-volume runs, multi-cavity molds are typically more cost-effective.
Using Modular or Family Molds
Modular molds and family molds allow manufacturers to produce multiple parts with a single mold, saving on tooling costs. Modular molds let manufacturers swap inserts to create different parts, while family molds combine multiple designs into one. Both approaches improve efficiency and reduce costs.
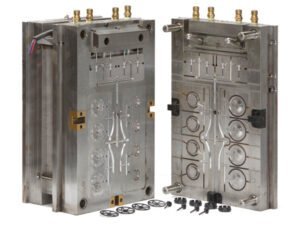
Mold Material Selection: Steel vs. Aluminum
Steel molds are durable and ideal for high-volume runs, although they have a higher initial cost. Aluminum molds are cheaper and faster to produce, making them suitable for short-run or low-volume production, though they wear out quicker. Choosing the right material balances initial investment with production needs.
Determining the Right Production Volume
Choosing the right production volume is key to balancing low cost injection molding and product demand. Production volume impacts cost per unit, tooling expenses, and project feasibility.
How Batch Size Affects Cost per Unit
Batch size directly influences cost per unit. For low-volume production, tooling costs are distributed over fewer parts, resulting in higher per-unit costs. As production volume increases, these fixed costs are spread out, lowering the unit price. However, producing more than necessary can lead to excess inventory, so finding the right balance is essential.
Breaking Down the Relationship Between Tooling Costs and Unit Price
Tooling costs, such as mold fabrication and maintenance, are significant in injection molding. High-volume production reduces these costs per unit as the fixed tooling investment is spread across more parts. In contrast, low-volume production leads to higher per-unit tooling costs, as the investment is divided among fewer parts.
When to Choose Low-Volume vs. High-Volume Production Strategies
Low-volume production is ideal for prototypes, small batches, or custom parts. It’s best for uncertain demand or frequent design changes. High-volume production is more cost-effective for mass production, as tooling costs are distributed over a larger number of parts. The right strategy depends on project needs, demand, and budget.
Lowering Costs Through Supply Chain Optimization
Optimizing the supply chain is crucial for achieving low cost plastic injection molding. Streamlining sourcing, partnerships, and inventory management helps reduce overall production costs.
Sourcing Molds and Materials from Low-Cost Regions
Sourcing molds and materials from regions with lower production costs, like China or India, can significantly cut material and labor expenses, making inexpensive injection molding possible.
Working with Contract Manufacturers to Reduce Labor and Operational Costs
Outsourcing to contract manufacturers reduces in-house labor and operational costs. This allows manufacturers to leverage specialized expertise and economies of scale, driving down overall expenses for cost-efficient molding.
Just-in-Time (JIT) Manufacturing to Minimize Inventory Expenses
Just-in-Time (JIT) manufacturing minimizes inventory costs by producing parts only when needed, reducing waste and storage expenses. This approach contributes to cost-effective plastic injection molding by aligning production with demand.
Alternative Low-Cost Molding Technologies
As manufacturers continue to seek low cost plastic injection molding solutions, alternative molding technologies offer viable options for specific needs. These methods often provide cost savings and can be particularly useful for prototyping, low-volume production, and applications with specialized requirements.
Silicone Molding vs. Traditional Injection Molding: Pros, Cons, and Cost Comparison
Silicone molding is an attractive alternative to traditional injection molding for small runs, especially when flexibility and design complexity are needed. While silicone molding typically costs more in terms of mold creation due to the need for specialized silicone molds, it can be cheaper for low-volume productions. Traditional injection molding, on the other hand, has higher initial mold costs but becomes cost-effective at high volumes. However, silicone molding can provide faster cycle times and is ideal for flexible or soft components that would be difficult to achieve with standard injection molding.
Aspect | Silicone Molding | Traditional Injection Molding |
---|---|---|
Cost for Low-Volume Runs | Cheaper for low-volume productions | Higher initial mold costs, but becomes cost-effective at higher volumes |
Mold Creation | Requires specialized silicone molds, which are more expensive | Standard molds, but more expensive for complex designs |
Cycle Time | Faster cycle times | Longer cycle times compared to silicone molding |
Design Flexibility | Ideal for flexible or soft components, high design complexity | Suitable for rigid, standardized designs |
Material Versatility | Limited to silicone-based materials | Wide range of material options available |
Ideal Use Case | Small runs, parts needing flexibility and complexity | Large volume production, parts requiring higher rigidity |
3D Printing vs. Low-Pressure Injection Molding: When Additive Manufacturing is a Viable Alternative
For small production runs and prototypes, 3D printing can be a powerful tool. While it offers an extremely low initial cost, especially for one-off prototypes, it struggles with scalability and material limitations for larger production runs. Low-pressure injection molding, though initially requiring investment in molds, provides a more cost-efficient solution for low-volume production and greater material versatility. The trade-off between 3D printing and low-pressure injection molding comes down to part complexity, material properties, and production volume. Additive manufacturing is ideal for rapid prototypes, while low-pressure molding can offer more durable, production-grade parts.
Aspect | 3D Printing | Low-Pressure Injection Molding |
---|---|---|
Initial Cost | Very low initial cost, especially for prototypes | Requires investment in molds, higher initial costs |
Scalability | Struggles with scalability for large production runs | More scalable for low-volume production |
Material Options | Limited material selection | Greater material versatility and production-grade materials |
Speed of Production | Rapid for small runs and prototypes | Slower compared to 3D printing for prototypes, but faster for low-volume production |
Ideal Use Case | Rapid prototyping, one-off parts | Production of low-volume parts, more durable products |
Complexity Handling | High complexity and customization, ideal for intricate parts | Suitable for medium-complexity parts, but less intricate than 3D printing |
CNC Machining vs. Small-Batch Injection Molding: Cost-Effectiveness for Prototyping and Low-Volume Runs
When comparing CNC machining to small-batch injection molding, it’s crucial to consider part complexity and material requirements. CNC machining is better suited for prototyping, especially when highly detailed parts are needed, and no molds exist. However, for low-volume production, small-batch injection molding can be a more cost-effective solution. While the initial mold cost is higher than CNC, it offers a much faster production rate for repetitive parts. Small-batch injection molding is ideal when consistent quality is required for small orders, while CNC machining offers flexibility for intricate designs without mold costs.
Aspect | CNC Machining | Small-Batch Injection Molding |
---|---|---|
Ideal Use Case | Prototyping, parts requiring intricate details | Low-volume production runs with consistent quality |
Initial Cost | No mold costs, higher hourly machining rates | Higher mold costs, but faster production for repetitive parts |
Production Speed | Slower due to manual processes and limited automation | Faster, particularly for repeated small orders |
Material Options | Flexible, can work with almost any material | Limited to injection-molding materials |
Production Volume | Best suited for one-off or small-batch prototypes | More cost-effective for small runs, less so for larger productions |
Part Complexity | Best for high-complexity designs | Good for medium-complexity designs that require consistency |
Balancing Cost and Quality in Plastic Injection Molding
When aiming for low cost plastic injection molding, balancing cost efficiency with product quality is crucial. By choosing the right materials, optimizing mold design, and considering alternative molding technologies, manufacturers can significantly reduce production costs. However, it is equally important to ensure that these cost-saving measures do not compromise the integrity or performance of the final product.
Key takeaways include understanding the relationship between production volume and tooling costs, and selecting the appropriate molding method based on project requirements. Small-batch injection molding, 3D printing, and other alternatives offer cost-effective solutions for low-volume production, while traditional methods can be more suitable for high-volume runs.
Ultimately, the goal is to ensure quality while adhering to budget constraints. This requires a strategic approach, including optimizing production processes, material usage, and supply chain management. By focusing on these areas, manufacturers can achieve a balance between affordability and high-quality outputs, ensuring a successful inexpensive injection molding process.