Products made by plastic molding are integral to countless industries, shaping the world around us with a wide variety of applications. From everyday household items to complex automotive components, plastic molding has revolutionized manufacturing by enabling the efficient production of durable, lightweight, and cost-effective products. This article delves into the diverse range of products created through plastic molding, exploring how this versatile process is applied across different sectors and highlighting the benefits it brings to modern manufacturing. Whether you’re designing consumer goods, automotive parts, or medical devices, understanding the power of plastic molding can unlock new possibilities for innovation and efficiency.
Injection Molding Design Features
Injection molding is a versatile manufacturing process that enables the production of a wide range of parts and components. By understanding various design features, engineers and manufacturers can optimize the functionality, cost-efficiency, and performance of injection-molded products. Next, we will explore several key design features commonly used in injection molding: snap fits, living hinges, threads, and underfills and cores.
Injection Molding Snap Fits
Snap fits are mechanical fasteners that are designed into the plastic part itself, allowing parts to be assembled without the need for additional fasteners, such as screws or bolts. They work by utilizing the flexibility of the plastic material to allow one part to “snap” into place within a corresponding feature on another part.
Snap Fits Application Examples
- Household Appliance Enclosures
- Electronic Device Assembly Parts
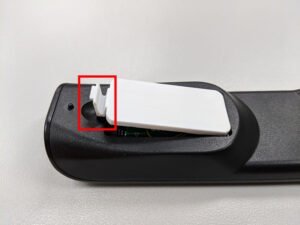
Injection Molding Living Hinges
Living hinges are thin, flexible sections of plastic that connect two parts of a product, allowing them to pivot or fold. These hinges eliminate the need for additional mechanical components and are an integral part of many plastic designs.
Living Hinges Application Examples
- Packaging Products
- Consumer Electronics
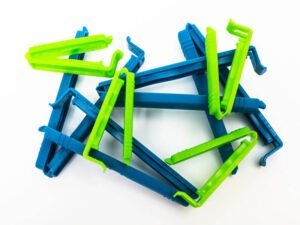
Injection Molding Threads
Threads are helical structures that allow two parts to be screwed together, providing a secure connection. In injection molding, both internal and external threads can be formed within plastic parts during the molding process.
Threads Application Examples
- Containers and Bottle Caps
- Medical Devices with Threaded Connections

Everyday Products Made Using Injection Molding
Injection molding is behind many of the products we use every day, making it one of the most versatile manufacturing processes in modern production.
Household Items
Bottles, Containers, and Kitchenware: Plastic molding is used extensively in the production of everyday household items like food containers, measuring spoons, and cutlery. These products are lightweight, durable, and easy to mold into different shapes, making them ideal for mass production.
Storage Bins and Organizers: From toy storage bins to closet organizers, plastic molding allows for the creation of functional and aesthetically pleasing storage solutions that can withstand the rigors of daily use.

Automotive Parts
Dashboard Components: Many components found in vehicle dashboards, including buttons, knobs, and housing for electronic devices, are made through injection molding. The process allows for high-quality, durable components that are resistant to wear and temperature fluctuations.
Bumpers and Interior Fittings: Plastic injection molding also plays a significant role in creating parts like car bumpers, interior fittings, and even exterior trim. These parts are lightweight and impact-resistant, contributing to both the safety and aesthetics of the vehicle.
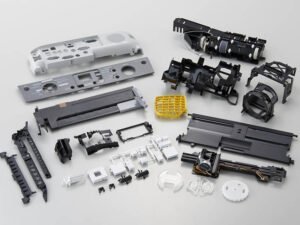
Electronics and Gadgets
Phone Cases and Covers: The injection molding process is essential in the production of phone cases and covers. These products must be precisely molded to ensure proper fit and protection, and the material used must be durable enough to withstand daily wear.
Chargers and Connectors: Connectors and chargers for a wide range of electronic devices, from smartphones to laptops, are often made using injection molding. This ensures a high level of durability and reliability for products that need to function under various conditions.
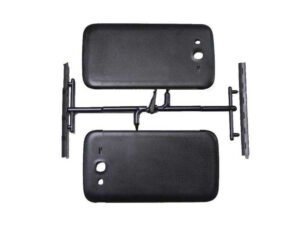
Medical Devices
Syringes and Surgical Tools: Injection molding is used extensively in the production of medical devices such as syringes, surgical tools, and diagnostic equipment. These products require high precision, safety, and compliance with medical regulations, all of which are made possible through injection molding.
Diagnostic Equipment and Disposable Products: From test tubes to diagnostic strips, plastic molding is crucial for producing single-use medical items that are both cost-effective and sterile. The molding process allows for the production of parts that are uniform and reliable.
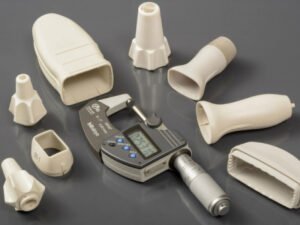
Consumer Goods
Toys, Combs, and Brushes: Toys, hairbrushes, and combs are commonly made from injection-molded plastic, offering affordability and the ability to produce large quantities in different shapes, sizes, and colors.
Furniture Components and Accessories: Plastic molding is also used to produce furniture components such as legs, knobs, and brackets. These components provide strength and durability while maintaining an appealing aesthetic.
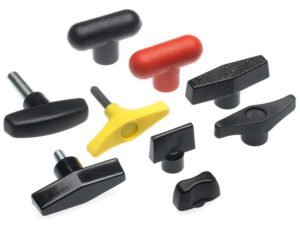
Packaging
Caps, Closures, and Medical Packaging: Plastic iPackanjection molding is critical in the production of packaging solutions, such as caps and closures for bottles, containers, and pharmaceuticals. The precision of the molding process ensures airtight seals and effective protection for the contents.
Plastic Bags and Clamshell Packaging: The production of plastic bags, clamshell packaging, and blister packs also relies on plastic molding, offering a cost-effective way to create transparent and durable packaging for a wide range of products.
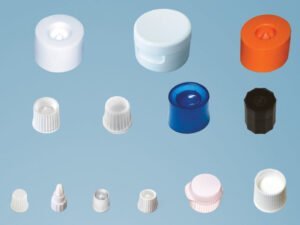
Key Benefits of Injection Molding
Injection molding offers several advantages that make it the preferred choice for mass production of plastic parts.
Cost-effectiveness in Mass Production
Injection molding is highly cost-efficient, especially when producing large volumes of identical parts. Once the mold is created, the cost per part decreases significantly, making it an ideal choice for mass production.
Precision and Repeatability of Molded Products
The high precision of the injection molding process allows for the production of parts with intricate details and tight tolerances. The ability to replicate these parts consistently ensures uniformity in large production runs, reducing the likelihood of defects.
Ability to Produce Complex Geometries
Injection molding can create parts with complex geometries that would be difficult or impossible to achieve with other manufacturing methods. Features such as thin walls, undercuts, and hollow sections can all be incorporated into the design without compromising strength or functionality.
Durability and Strength of Molded Plastic Parts
Plastic parts produced via injection molding are durable and have excellent mechanical properties. They are resistant to wear, impact, and environmental factors, which makes them suitable for a wide range of applications.
Conclusion
As a custom molding company, Injection molding is an indispensable process used to create a wide variety of products across multiple industries. From household items to critical medical devices, the versatility of injection molding has a profound impact on daily life. As technology continues to evolve, the future of injection molding looks promising, offering new materials, faster production methods, and sustainable solutions.