Types of casting processes are fundamental to the manufacturing industry. The casting not only in its ability to produce detailed parts but also in its cost-effectiveness and efficiency. By pouring molten materials into a mold, casting allows for the creation of complex shapes and intricate designs that would be difficult, if not impossible, to achieve through other manufacturing methods. Understanding the different types of casting processes available today is essential for selecting the right method for specific applications. Each process offers unique advantages and is suited for different materials and production needs. In this post, we will explore the different types of mould in casting, especially pu casting.
What is Casting Process?
Casting is defined as a manufacturing process where liquefied materials, such as molten metal or other substances, are poured into specially designed molds. Once the material cools and solidifies, it takes on the shape of the mold cavity, resulting in a finished product known as a casting. This process not only facilitates the creation of complex shapes but also enhances production efficiency by reducing the need for extensive machining or assembly. This method is pivotal in producing a wide range of products, from intricate artistic pieces to essential components in automotive and aerospace industries.
In modern times, casting remains a vital component of manufacturing processes globally. It is estimated that castings are found in approximately 90% of durable manufactured goods.
The Main Steps in the Casting Process
Mold Preparation: The first step involves creating a mold based on the part to be cast. Molds are typically made from materials such as wood, metal, or other substances, and their design must consider the shape and size of the casting. The mold-making process may involve using sand, plaster, or ceramic materials, depending on the chosen casting method.
Melting the Metal: Next, the selected material is heated to its melting point to transform it into a liquid state. It is crucial to ensure that the material is completely melted to facilitate a smooth pouring process in the subsequent steps.
Pouring: The molten metal is then poured into the prepared mold. This step requires careful handling to avoid the formation of bubbles and other defects. Once poured, the mateial fills the mold cavity, taking on the basic shape of the casting.
Cooling and Solidification: The liquid material cools and gradually solidifies within the mold, forming a solid casting. The cooling time depends on factors such as the thickness of the casting and the type of material used. During this phase, shrinkage may occur, so it is important to account for this in mold design.
Defect Inspection and Finishing: After cooling, the casting is inspected for any potential defects, such as porosity, cracks, or surface irregularities. If necessary, post-processing techniques (such as grinding or welding) can be employed to enhance the quality and appearance of the casting.
Materials Required for Casting
Casting is a versatile manufacturing process that utilizes a variety of materials to create components across different industries. Common Materials Used in Casting
PU: Polyurethane (PU) is an increasingly popular casting material. PU can be formulated to achieve a wide range of hardness levels, from soft rubber-like materials to rigid plastics.
Plastics: These bendable materials can be molded through casting, too.
Rubber: For elasticity and flexibility parts manufacturing, rubber is a good materials selection.
Metals and Alloys: Metals are a popular choice for casting due to their strength and durability. Such as iron, aluminum, copper, and zinc.
Epoxy Resins: Epoxy resins are used in casting for their strong adhesion and chemical resistance. They are often employed in applications requiring durable and precise components, such as electronic housings and automotive parts.
Concrete: Concrete is frequently used for larger castings, such as architectural elements or sculptures. Its ability to be molded into various shapes makes it a versatile material in construction.
Gypsum: Gypsum is commonly used in the production of molds and casts, particularly in artistic applications.
14 Types of Casting Processes
There are different types of casting processes, and each casting type has its own advantages and applications as per customer’s requirement. Here, we explore the 14 types of casting processes.
1. Sand Casting

Sand casting, also known as sand molding casting, is one of the most common casting types. It involves creating a mold from a mixture of sand and a binder, which is then formed into a mold cavity.. The mold is formed around a pattern that represents the desired shape of the final product. Once the mold is prepared, molten metal is poured into it and allowed to cool and solidify. sand casting accounts for about 60% of all metal castings produced today.
Advantages of Sand Casting:
- Cost-effective: Sand casting is one of the most economical casting methods, especially for large parts.
- Versatility: Suitable for a wide range of materials and alloys.
- Large parts: Capable of producing large castings, with some molds able to accommodate parts weighing several tons.
Applications: Commonly used in the automotive industry for components such as engine blocks, cylinder heads, and pump housings.
2. PU Casting (Urethane Casting)

PU casting, also known as urethane casting service, involves using polyurethane materials to create parts and components. This process typically utilizes a master pattern, often produced via 3D printing, to create a silicone mold. The polyurethane resin is then poured into the mold to form the final product. Urethane casting is particularly valued for its ability to replicate intricate details and surface textures from the original pattern.
Advantages of PU Casting:
- High Precision: Urethane casting can achieve exceptional levels of precision and accuracy, ensuring that cast parts meet tight tolerances and high-quality standards. This capability makes it ideal for applications where detail is critical.
- Flexibility in Design: The process allows for significant design flexibility, enabling manufacturers to produce parts with complex geometries that may be challenging or impossible to achieve with traditional methods like injection molding.
- Rapid Turnaround: Urethane casting offers a fast turnaround time compared to other manufacturing processes. Parts can often be produced and delivered within weeks, making it suitable for prototyping and small production runs.
- Low Tooling Costs: The use of silicone molds in urethane casting significantly reduces tooling costs compared to metal molds required for injection molding. This makes it an economical choice for low-volume production.
- Material Variety: A wide range of polyurethane formulations is available, allowing for the production of parts with varying properties, including rigidity, flexibility, and color options. This versatility enables manufacturers to tailor materials to specific application requirements.
Applications of PU Casting: PU casting is widely used across various industries due to its versatility and efficiency. Such as prototyping, housings, enclosures, that require durability and precision, etc.
3. Die Casting

Die casting is a manufacturing process that involves injecting molten materials into a mold (also known as a die) under high pressure. This method is primarily used for non-ferrous materials, such as aluminum, zinc, and magnesium. The die is typically made from hardened steel and can be reused for multiple casting cycles, making it suitable for high-volume production. The process allows for the creation of complex shapes with fine details and thin walls.
Advantages of Die Casting:
- Die casting produces parts with exceptional precision and tight tolerances, often within ±0.005 inches.
- The process results in a smooth surface finish (typically around 125 RA), which can reduce or eliminate the need for additional surface treatment.
- Die casting is capable of producing large quantities of parts quickly due to its efficient cycle times.
- The die casting process generates minimal waste compared to other methods.
Die casting allows for the production of intricate shapes with complex geometries.
Applications: Die casting has a wide range application such as electronic housing, automotive parts, industrial equipment, etc.
4. Pressure Die Casting

Similar to die casting but involves injecting molten metal under high pressure into a mold to create complex shapes quickly.
Advantages of pressure die casting:
- High production efficiency with excellent repeatability.
- Ideal for high-volume manufacturing.
Applications: Commonly found in automotive parts, electronic housings, and appliances.
5. Investment Casting (Lost-Wax Casting)

Investment casting also known as lost wax casting. It involves creating a wax pattern coated with a ceramic shell. The wax is melted away to leave a mold for pouring molten metal.
Advantages of investment casting:
- High precision and excellent surface finish.
- Capable of producing intricate designs and thin-walled sections.
- Versatile for various materials.
Applications: Common in aerospace, medical devices, and jewelry manufacturing.
6. Permanent Mold Casting

Uses reusable metal molds instead of sand molds to cast parts. The molten metal is poured into these molds for cooling.
Advantages of permanent mold casting:
- Better surface finish and dimensional accuracy compared to sand casting.
- Suitable for higher volume production runs.
Applications: Often used in automotive components and industrial machinery.
7. Centrifugal Casting

Molten metal is poured into a rotating mold, utilizing centrifugal force to distribute the metal evenly.
Advantages of centrifugal casting:
- Produces dense and strong cylindrical parts with fewer defects.
- Efficient for producing large quantities of similar components.
Applications: Used for pipes, tubes, and other cylindrical shapes in various industries.
8. Plaster Casting

A process where plaster is used to create molds for casting materials. The plaster mold captures fine details well.
Advantages of plaster casting:
- Excellent surface finish and detail reproduction.
- Suitable for small production runs.
Applications: Commonly used in artistic applications and small mechanical parts.
9. Vacuum Casting

A vacuum is applied to draw molten metal into the mold cavity, enhancing flow and reducing defects.
Advantages of vacuum casting:
- Improved dimensional accuracy and surface quality.
- Ideal for intricate parts with tight tolerances.
Applications: Used in aerospace components and precision engineering.
10. Continuous Casting

Continuous casting, also known as strand casting, In continuous casting, molten material is poured into a mold that is cooled by water. The process allows the metal to solidify while being continuously drawn from the mold. This continuous flow results in long lengths of metal that can be cut into desired sizes later.
Advantages of continuous casting:
Continuous casting significantly reduces production time by combining multiple steps of traditional casting processes into one seamless operation.
- The process ensures uniformity in cross-section and composition, resulting in fewer defects such as porosity and segregation.
- The controlled cooling rates enhance grain structure and mechanical properties of the cast product.
- Automation in continuous casting reduces labor requirements compared to traditional methods, contributing to overall cost-effectiveness.
Applications: The continous casting common producing semi-finished products like billets, blooms, or slabs for further processing.
11. Gravity Die Casting

Involves pouring molten metal into a stationary mold under the force of gravity without pressure assistance.
Advantages of Gravity die casting:Cost-effective for medium-volume production with good surface quality.
Applications: Commonly used in manufacturing various industrial components.
12. Lost Foam Casting
A foam pattern is used to create a mold that vaporizes when molten metal is poured in, forming the part directly from the foam shape.
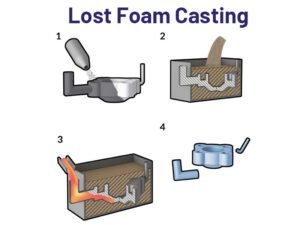
Advantages of lost foam casting:Allows for complex geometries without the need for core inserts or additional machining.
Applications: Used in automotive parts and complex industrial components.
13. Low Pressure Casting

Utilizes low pressure to fill the mold with molten metal, allowing for better control over the filling process.
Advantages of low pressure casting:Reduces gas porosity and improves surface quality compared to traditional methods.
Applications: Suitable for large castings such as engine blocks.
14. Squeeze Casting

Combines casting with forging by applying pressure to the molten metal in the die to enhance density and strength.
Advantages of squeeze casting:Produces parts with superior mechanical properties and dimensional accuracy.
Applications: Used in aerospace components and heavy machinery.
Differences Between Casting and Injection Molding
The injection molding process also is the process that injecting the molten material in the mold cavity. But, the process details, capabilities, materials are different from the casting molding. Next we will compare the casting molding and injection molding.
Fundamental Principles
Casting: Casting involves pouring molten material (typically metal) into a mold, allowing it to solidify into the desired shape. This process can utilize gravity or pressure to fill the mold cavity. For example, sand casting relies on gravity to pour the molten metal, while pressure die casting injects molten metal at high pressure to ensure complete mold filling.
Injection Molding: In contrast, injection molding involves injecting molten plastic into a closed metal mold under high pressure. The liquid plastic is forced into the mold cavity, where it cools and solidifies into a specific shape. This method is primarily used for thermoplastics and thermosets, which require low viscosity materials to flow easily during injection.
Production Efficiency and Cost Comparison
Tooling Costs: The tooling costs for casting are generally lower than those for injection molding. Casting molds can be simpler and less expensive to produce because they do not require the complex systems needed to regulate temperature and material flow in injection molding. For example, casting molds can be open or closed designs, providing flexibility in product design without incurring high costs.
Production Speed: Injection molding typically offers faster production rates due to its efficient cycle times. Once the mold is created, injection molding can produce hundreds or thousands of parts quickly, making it ideal for high-volume production runs.
Application and Product Characteristics Comparison
Product Types: Casting is commonly used for producing metal components such as engine blocks, industrial machinery parts, and intricate designs that require high strength and durability. On the other hand, injection molding is used primarily for plastic products like toys, consumer electronics housings, and automotive interior components.
Performance Characteristics: Cast products tend to exhibit higher mechanical strength and durability compared to injection-molded parts made from plastics. However, injection molding allows for greater design flexibility with complex shapes and multiple materials in a single run. Additionally, injection-molded parts often have smoother finishes and more consistent quality due to the controlled environment of the injection process.
Outsourcing Your PU Casting Needs to Flexiparts
Flexiparts is a professional manufacturer supply polyurethane (PU) casting services. The types of products we can manufacture include automotive components, industrial equipment parts, consumer products, etc.
In summary, outsourcing your PU casting needs to Flexiparts not only provides access to high-quality manufacturing capabilities but also enhances your overall production efficiency. By partnering with Flexiparts, you can leverage our expertise in PU casting services to meet your specific needs while ensuring that your products stand out in the competitive marketplace.