Types of molds in injection molding solution play a crucial role in determining production efficiency, cost, and part quality. From two-plate and three-plate molds to hot runner and cold runner systems, each mold type serves a specific purpose, influencing cycle times and material usage. Factors such as production volume, functionality, and material selection further dictate whether prototype molds, multi-cavity molds, insert molds, or specialized options like gas-assisted or stack molds are the best fit. Understanding these variations helps manufacturers optimize tooling investments, improve part consistency, and enhance overall manufacturing efficiency. In this post, we will introduce injection molds types in different classifications.
Classification Based on Mold Structure
Two-Plate Molds
Two-plate molds are the most common types of injection molds and consist of a fixed and a moving half. The parting line divides these halves, allowing the molded part to be ejected when the mold opens. These molds are simple, cost-effective, and suitable for a wide range of applications. However, their design may lead to gate vestiges on the part, which might require post-processing.
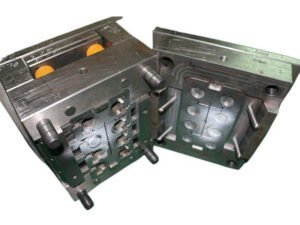
Three-Plate Molds
Three-plate molds incorporate an additional plate, allowing for more flexible gating options. Unlike two-plate molds, these molds separate the runner system from the finished part during ejection, eliminating the need for manual runner removal. This structure is ideal for complex components requiring precise gating but comes with increased tooling costs and maintenance requirements.
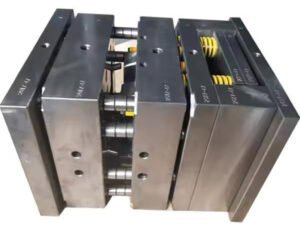
Hot Runner Molds
Hot runner molds utilize a heated manifold system to keep the molten plastic at the right temperature, ensuring consistent flow into the cavities. By eliminating cold runners, these molds reduce material waste and enhance production efficiency. They are ideal for high-volume manufacturing but require sophisticated temperature control systems and higher initial investment.
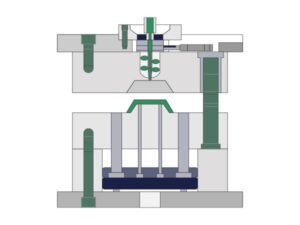
Cold Runner Molds
Cold runner molds rely on a system of channels to direct molten plastic into the mold cavities. After each cycle, the runner solidifies along with the part and is either manually removed or reground for reuse. While these molds have lower upfront costs compared to hot runner systems, they generate material waste and can lead to longer cycle times.

Key Structural Components of Injection Molds
While different types of molds in injection molding vary in complexity, they all share fundamental components that determine their performance.
1. Mold Base and Cavity/Core Inserts
The mold base serves as the foundation, holding all other components in alignment. It consists of multiple plates that house the cavity and core inserts, which define the external and internal shapes of the molded part.
- Cavity (A-Side): Forms the exterior surface of the plastic part.
- Core (B-Side): Creates the interior geometry, including undercuts or hollow sections.
- Interchangeable Inserts: Allow for design modifications without reworking the entire mold, reducing production downtime.
2. Ejection System
Once the plastic part solidifies, it must be efficiently removed from the mold. The ejection system prevents defects like warping and ensures smooth demolding.
- Ejector Pins: Strategically placed to apply even pressure while pushing out the part.
- Sleeve Ejectors: Used for cylindrical or hollow parts, applying force around the circumference.
- Air Ejectors: Blow compressed air into the cavity to release lightweight or delicate parts.
- Stripper Plates: Distribute ejection force evenly across large surface areas to prevent deformation.
3. Cooling System
Temperature regulation is critical in injection molding mold types to control shrinkage, cycle time, and part consistency. Cooling channels must be precisely designed to optimize heat dissipation.
- Conformal Cooling Channels: Follow the shape of the mold cavity, ensuring uniform cooling and reducing warpage.
- Baffles and Bubblers: Improve cooling efficiency in deep or complex mold sections.
- Oil or Water Circulation: Used depending on required thermal control precision.
4. Gating and Runner System
The flow of molten plastic into the mold is controlled by the gating system, which consists of runners, sprues, and gates. This system is critical in managing material distribution and minimizing waste.
- Cold Runners: Transport material from the sprue to the cavity, typically removed and recycled after molding.
- Hot Runners: Maintain plastic in a molten state, eliminating excess waste and improving cycle times.
- Gate Types: Direct gates, edge gates, and submarine gates impact material flow and part finish.
5. Venting System
Trapped air during injection can lead to burn marks, voids, or incomplete fills. A well-designed venting system prevents these defects by allowing air to escape as the cavity fills.
- Micro Vents: Precision-cut openings along the parting line to release trapped gases.
- Porous Steel Inserts: Enable gas to dissipate without additional venting channels.
- Vacuum-Assisted Molding: Actively removes air to ensure defect-free parts.
Classification Based on Production Volume
Prototype Molds
Prototype molds are designed for short production runs, typically used to test part designs before full-scale manufacturing. These molds are often made from softer materials such as aluminum or soft steel, allowing for quick modifications. While not intended for high-volume production, prototype molds play a critical role in validating designs and avoiding costly errors in later stages.
Production Molds
Production molds are built for long-term, high-volume manufacturing. Constructed from hardened steel, these molds withstand thousands to millions of cycles without significant wear. They offer superior durability, precision, and consistency, making them ideal for large-scale industrial applications. However, their initial cost is high due to the extensive machining and engineering required.
Classification Based on Application and Functionality
Single-Cavity Molds vs. Multi-Cavity Molds
Single-cavity molds produce one part per injection cycle, making them ideal for low-volume production, prototyping, or manufacturing high-precision components. They offer better process control, lower tooling costs, and easier maintenance but result in slower production rates.
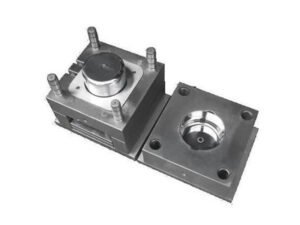
Multi-cavity molds, on the other hand, have multiple identical cavities, allowing for the simultaneous production of several parts per cycle. These molds significantly increase output and reduce the cost per part in high-volume manufacturing. However, they require precise balancing to ensure even material distribution and can have higher tooling costs.
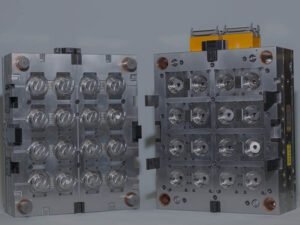
Family Molds
Family molds are molds with multiple cavities that produce different but related parts in a single cycle. They are suitable for projects requiring the simultaneous production of various components, reducing assembly time and improving production efficiency. The advantages of family molds include high flexibility and simplified assembly processes. However, they have a higher initial cost, require more complex maintenance, and can be challenging to maintain consistent quality across different parts.
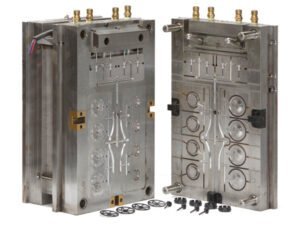
Insert Molds
Insert molding integrates metal or plastic components into the injection molding process, creating hybrid parts without secondary assembly. The mold holds pre-placed inserts—such as threaded brass fittings or electronic connectors—while molten plastic flows around them, forming a durable bond. This technique enhances strength, reduces assembly costs, and improves part reliability.

Overmolds
Overmolding involves molding one material over another, typically to add functionality or aesthetics. A soft elastomer (such as TPE) can be molded over a rigid plastic (like ABS) to create comfortable grips, seals, or vibration-resistant housings. This process ensures strong adhesion between layers, eliminating the need for adhesives or mechanical fasteners.

Specialized Injection Mold Types
Unscrewing Molds
Unscrewing molds are designed for threaded plastic parts, such as bottle caps or threaded connectors. These molds incorporate rotating mechanisms that allow the molded part to be unscrewed during ejection rather than being forcefully pulled out. This prevents thread damage and ensures high precision in threaded components.
Gas-Assisted Injection Molds
Gas-assisted injection molding uses controlled gas injection to create hollow sections within thick-walled parts. This technique reduces material usage, minimizes sink marks, and improves dimensional stability. Common applications include automotive handles, furniture, and appliance housings.
Stack Molds
Stack molds consist of multiple parting surfaces, allowing multiple levels of cavities to operate in a single molding cycle. By effectively doubling or tripling output without increasing clamping force requirements, stack molds optimize efficiency for high-volume production. They are commonly used for packaging, medical components, and consumer goods.

Rotational Molds
Rotational molds, while not a traditional injection molding type, utilize rotational motion and heat to evenly distribute plastic material inside a mold. This method is ideal for large, hollow products such as tanks, containers, and playground equipment. Unlike standard injection molding, rotational molding requires longer cycle times but offers cost-effective solutions for large-scale parts.
Material Selection for Injection Molds
Steel Molds vs. Aluminum Molds
The choice between steel molds and aluminum molds significantly impacts production efficiency, cost, and durability.
Steel molds—typically made from hardened tool steel (such as P20, H13, or stainless steel variants)—are known for their exceptional strength, wear resistance, and longevity. They withstand high-pressure injection molding cycles, making them ideal for large-scale production where mold longevity and precision are critical. While steel molds have a higher initial cost and longer lead time, their durability ensures lower long-term maintenance costs.
Aluminum molds, by contrast, offer a more cost-effective solution for low-to-medium production runs, rapid prototyping, and short-cycle production. Aluminum conducts heat faster than steel, reducing cooling times and improving cycle efficiency. However, aluminum molds wear out faster under high pressures and may require reinforcement for complex or high-volume applications.
Factors Affecting Material Choice
Several key factors influence the selection of mold materials:
- Production Volume – High-volume production demands steel molds for durability, while aluminum molds are suitable for prototyping and limited runs.
- Part Complexity – Detailed features and tight tolerances often require steel molds due to their ability to maintain precision over repeated cycles.
- Cycle Time – Aluminum molds dissipate heat faster, leading to shorter cycle times, which is advantageous in fast-paced production environments.
- Cost Considerations – Steel molds have a higher upfront investment but lower per-part costs in mass production, whereas aluminum molds are budget-friendly for smaller projects.
- Material Compatibility – Certain plastics, particularly those with abrasive fillers, can wear down aluminum molds quickly, necessitating steel molds for extended use.
- Tooling Maintenance – Steel molds demand minimal repairs over their lifespan, while aluminum molds require more frequent maintenance to prevent degradation.
How to Choose the Right Mold Type for Your Project?
Choosing the right mold type is crucial for ensuring the quality, efficiency, and cost-effectiveness of your manufacturing process. The selection depends on factors such as material requirements, production volume, product complexity, budget, and durability expectations. Understanding the different mold types and their applications will help you make an informed decision.
Consider the Type of Molding Process
The first step in selecting a mold is determining the molding process you will use. Different molding methods require different mold types. For example:
- Injection Molding Molds are used for high-precision, mass-produced plastic parts.
- Compression Molding Molds are designed for thermoset materials and rubber products.
- Blow Molding Molds are used to create hollow objects like bottles and containers.
- Rotational Molding Molds are suitable for large, hollow, and seamless plastic parts.
- Extrusion Molds (Dies) shape continuous profiles such as pipes and sheets.
- Thermoforming Molds are used for thin-walled plastic sheets that are heated and formed over a mold.
Determine the Production Volume
Production volume significantly impacts the mold type selection:
- High-volume production (hundreds of thousands to millions of units): Use a durable, high-precision mold made of hardened steel.
- Medium-volume production (10,000 to 100,000 units): Use a semi-hardened steel mold, which balances durability and cost.
- Low-volume production (fewer than 10,000 units): Use aluminum or soft steel molds, which are more affordable and easier to modify.
For prototype development, 3D-printed molds or silicone molds may be used for rapid testing before committing to full-scale production.
Assess Mold Material Options
Molds can be made from different materials, each with its advantages:
- Hardened Steel Molds: High durability, excellent for large production runs, but expensive.
- Pre-hardened Steel Molds: Less expensive than fully hardened steel but has a shorter lifespan.
- Aluminum Molds: Lower cost, faster manufacturing, and good for low-volume production, but less durable.
- Silicone Molds: Used for prototyping and short-run production of flexible materials.
Consider Product Complexity and Design Features
Complex designs require specialized molds with additional features:
- Multi-cavity molds: Increase production efficiency by producing multiple parts in one cycle.
- Family molds: Produce different parts in the same mold for cost-saving.
- Hot runner molds: Reduce material waste by eliminating runners in injection molding.
- Cold runner molds: More affordable but generate more material waste.
- Two-shot or multi-shot molds: Allow molding of multiple materials or colors in a single cycle.
Budget and Lead Time Considerations
The cost of mold fabrication depends on material choice, complexity, and required precision. Steel molds take longer to manufacture but last longer, making them suitable for mass production. Aluminum molds, while cheaper and faster to produce, have a shorter lifespan and may require frequent replacement.
Conclusion
Understanding the types of molds in injection molding is crucial for balancing cost, efficiency, and product quality. Choosing between two-plate, three-plate, hot runner, or cold runner molds, as well as single-cavity vs. multi-cavity configurations, depends on production volume, material selection, and budget. Steel molds offer durability for high-volume manufacturing, while aluminum and prototype molds provide flexibility for short runs. Cost considerations extend beyond initial investment to maintenance, cycle times, and long-term efficiency. Selecting the right injection molding mold types ensures precision, reduces defects, and optimizes production, ultimately enhancing scalability and profitability in plastic manufacturing.