Custom Injection Molding
Injection molding is an important process in custom components manufacturing, guaranteeing the creation of your unique designs with precision and efficiency.
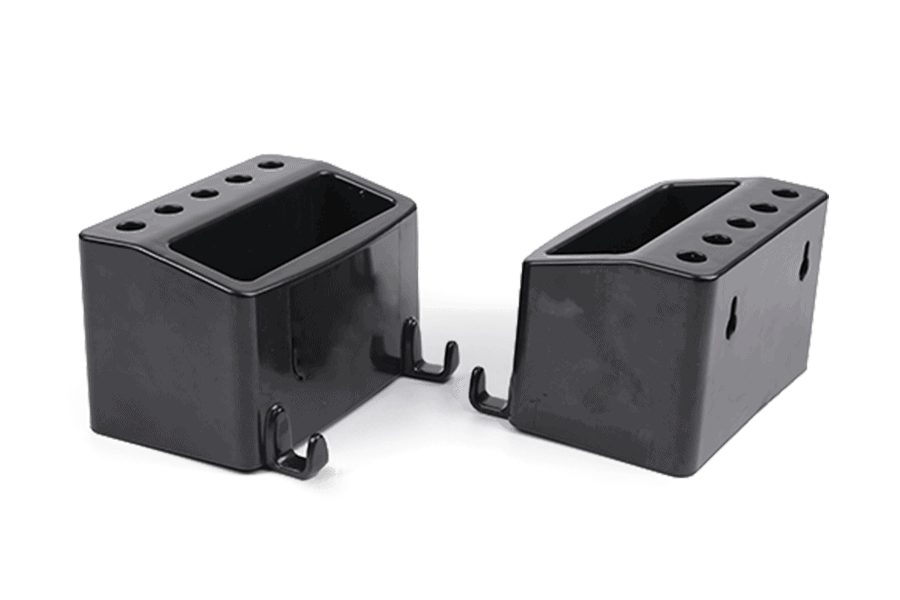
What is Injection Molding?
Injection molding is a widely-used manufacturing process for creating large volumes of plastic and rubber parts. It’s especially suited for mass production, where the same part is produced thousands or even millions of times in succession. This efficient and precise method allows for the cost-effective production of custom parts. Injection molding products can be found in commercial, consumer, and industrial settings. Injection molding parts offers businesses the opportunity to custom design parts or items with details that are unique to their brand.
Our Available Injection Molding Products
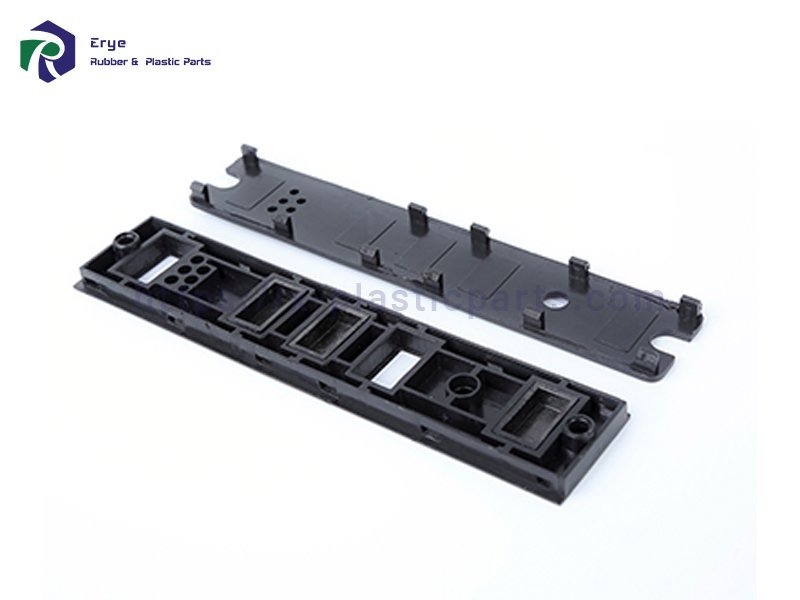
Plastic injection molding
Our plastic injection molding service excels in producing a wide range of plastic parts for various industries, delivering cost-effective and high-quality results.

Rubber injection molding Parts
With our rubber injection molding service, we create custom rubber parts with precision and durability. This option is ideal for applications requiring flexible and resilient components.

Overmolding serivce
Overmolding combines multiple materials to create complex parts. It enhances functionality and aesthetics, making it suitable for products requiring added layers or grips.

Insert molding service
Insert molding integrates metal or other materials into plastic or rubber parts during the molding process. It's a cost-effective way to enhance strength and functionality.

Large part injection molding service
Our large part injection molding service is designed to produce oversized components. It's perfect for manufacturing larger parts without compromising quality or precision.

Polyurethane Injection Molding Products
Molten polyurethane is injected into a closed mold at high pressure. The high-pressure forces the polyurethane to completely fill the mold cavity.
Custom Plastic Parts
Custom Rubber Parts
Materials for Custom Injection Molding Product
Plastic injection molding materials come in a variety of shapes and sizes, each having a different purpose.Injection molding is a typical method of thermoplastic production. Material selection is challenging, despite the fact that numerous common plastics can be used for injection molding.
15 years of professional engineers offer a wide range of injection molding material options, from adaptive plastics to flexible rubber. Meet your unique needs and specifications.
Plastic
- Polyethylene (PE)
- Polypropylene (PP)
- Polyvinyl Chloride (PVC)
- Polystyrene (PS)
- Acrylonitrile Butadiene Styrene (ABS)
- Polycarbonate (PC)
- Polyamide (Nylon)
- Polyformaldehyde (POM)
Rubber
- Ethylene Propylene Diene Monomer (EPDM)
- Styrene-Butadiene Rubber (SBR)
- Nitrile Rubber (NBR)
- Natural Rubber (NR)
- Silicone Rubber
- Fluoroelastomers (Viton)
- Neoprene
- Fluoroelastomers
Related Resources
Our Available Material
Injection Moulding Working Process
To obtain a high-quality, flawless injection molding product, a professional and scientific injection moulding process is required.
- Clamping: The mold, typically made of metal, is securely closed and clamped under high pressure to prevent material leakage.
- Injection: Molten material, usually plastic, is forced into the mold cavity through a nozzle and into the mold’s channels or runners.
- Cooling: The mold is cooled, helping the material solidify and reducing cycle time.
- Ejection: The mold opens, and the newly formed part is ejected using ejector pins or plates.
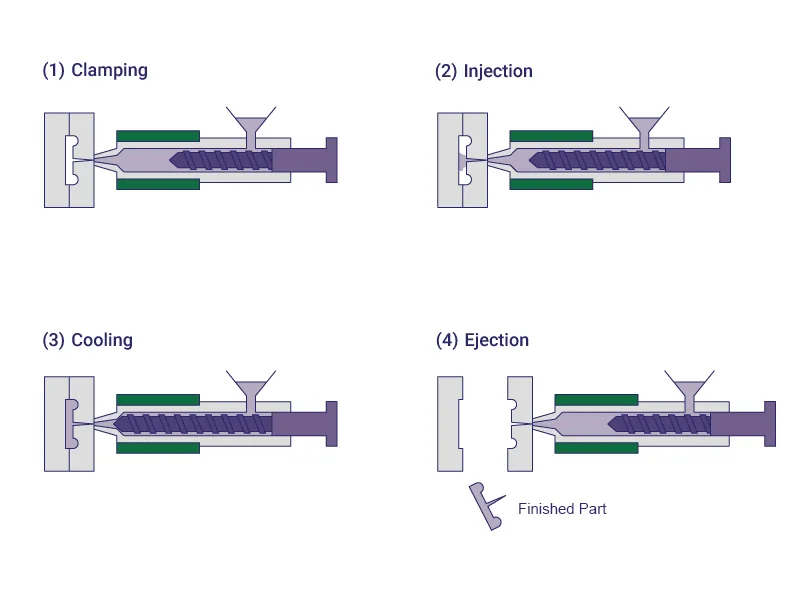
LET’S START A NEW INJECTION MOLDED PARTS
Application and Injection Molding Product
- Agriculture: OEMs designing for the agricultural market are turning to plastics as a low-cost alternative to metal parts commonly used throughout the industry. Plastics offer greater resistance to impact and moisture during use, as well as the ability to withstand extreme heat or cold.
- Toys: The most common example of an injection molded product in toys is the famous bricks made by LEGO®. These plastic bricks are made from ABS – a lightweight material that is very easy to mold and has high impact resistance.
- Mechanical and auto parts: Bumpers, dashboards, radio controls, cup holders, and many other elements in cars and transportation vehicles, are manufactured through the injection molding process. Common molding materials of choice for automobiles include nylon, polypropylene, PVC, and ABS.
- Medical industry: Items such as syringes, surgical instruments, and diagnostic equipment are often made using the injection molding process to ensure precision and sterility. Silicone, acrylonitrile butadiene styrene (ABS), polypropylene, and polyethylene are all common materials used in medical devices.
Some of the injection molding products produced by Flexiparts Plastic injection molding Factory:
Consumer Goods
- Toys
- Game controllers
- Toilet seats
- Cell phone cases
- Bakeware
- Cutting boards
- Plastic kitchen utensils
Commercial Construction
- Conduits for Concrete Beams
- Insulators
- Raised Flooring Panels
Residential Construction
- Electrical plugs
- Electrical switches
- Roof vents
- Deck fasteners
Sporting Goods
- Training Device
- Exercise Tools
- Helmets
- Protective padding
- Mouth guards
Automotive
- Car bumpers
- Dashboards
- Radio buttons
- Window controls
- Drink holders
Medical
- Syringes and other drug delivery equipment
- Housings on medical devices
- Laboratory and facility equipment
- Orthopedics
Why You Should Choose Injection Molding Service?
Injection molding excels in efficient mass production while maintaining quality
Injection moulding is a manufacturing powerhouse when it comes to producing large quantities of parts without compromising on quality. This process is renowned for its ability to efficiently churn out precise components at scale, making it a cost-effective choice for businesses aiming for both quantity and quality.
Consistent commitment to quality assurance
Injection molding assures exceptional quality through rigorous control in each production step, minimizing defects, ensuring long-term reliability, and maintaining a consistent commitment to excellence.
Able to achieve precision in manufacturing complex geometries
Injection moulding's precision is not limited to simple shapes. It excels in producing complex geometries with remarkable accuracy. This capability opens up a world of design possibilities, making it the ideal choice for industries demanding intricate parts.
Streamlining production with minimal post-processing
Injection molding's precision is not limited to simple shapes. It excels in producing complex geometries with remarkable accuracy. This capability opens up a world of design possibilities, making it the ideal choice for industries demanding intricate parts.
What is Downside to Injection Molding Service?
High Tooling Costs Can Impact Budgets Significantly:
Injection molding often requires the creation of custom molds, which can be expensive. These upfront costs can strain budgets, especially for small-scale production or prototypes.
Small Design Errors Can Lead to Costly Revisions
Precision is paramount in injection molding. Even minor design flaws can result in costly rework or mold adjustments. Attention to detail during the design phase is crucial.
Material Selection Complexity Requires Careful Consideration:
Choosing the right material for your injection molding project can be challenging. Each material has unique properties, and selecting the wrong one can affect product quality and performance.
Uniform Wall Thickness Is Critical for Proper Molding
Maintaining consistent wall thickness in molded parts is essential for quality. Variations can lead to defects and inconsistencies in the final product.
Injection Molded Products We Made



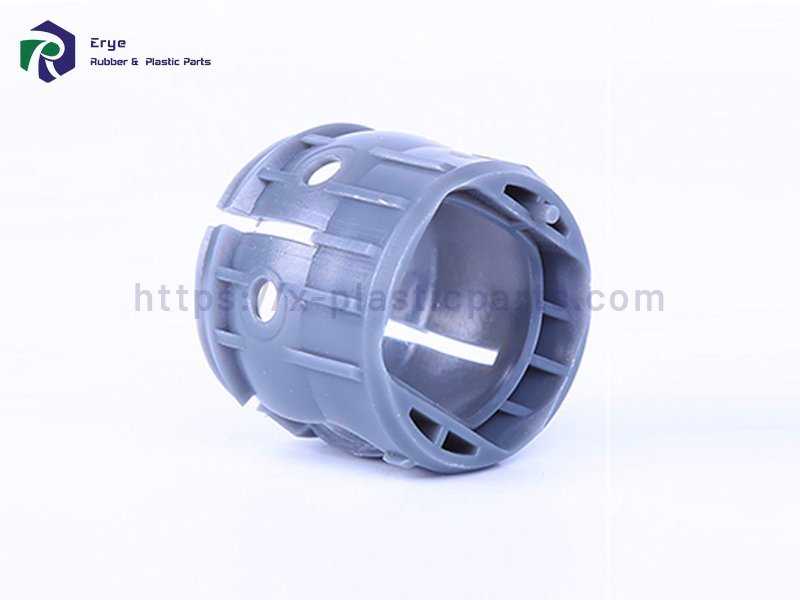
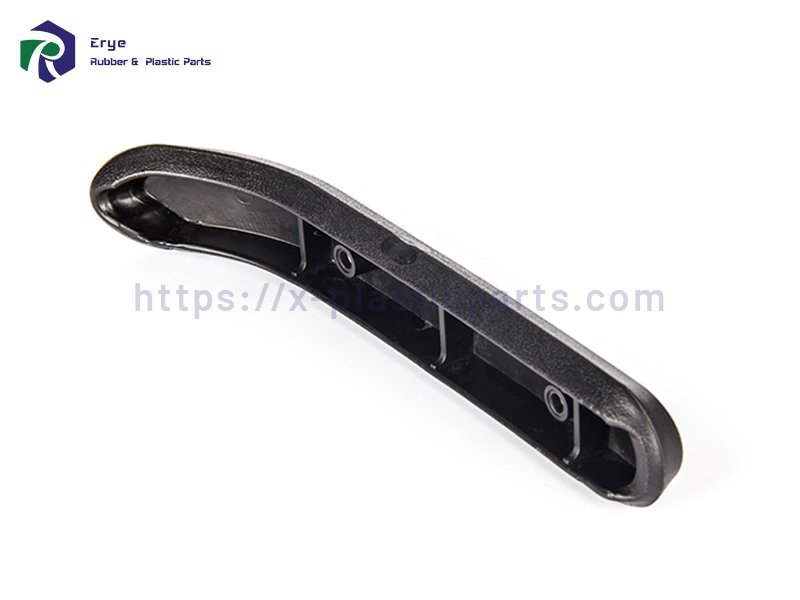
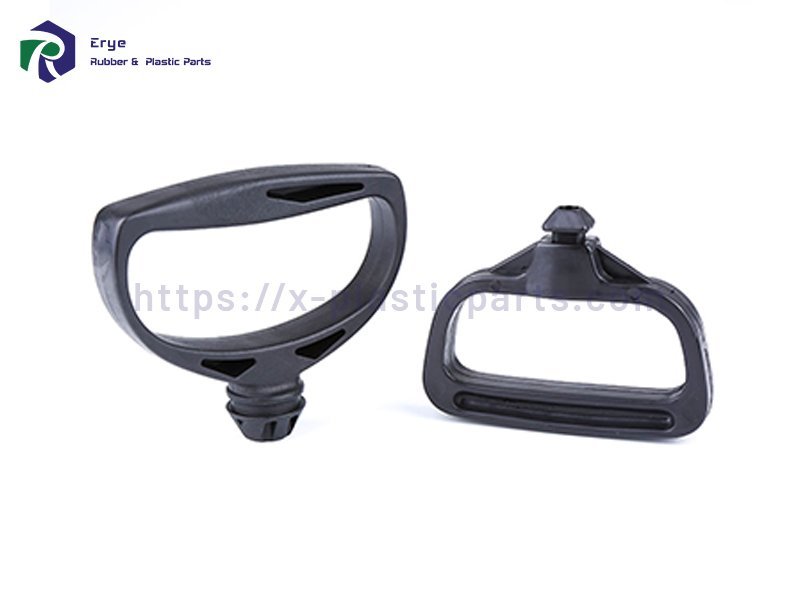

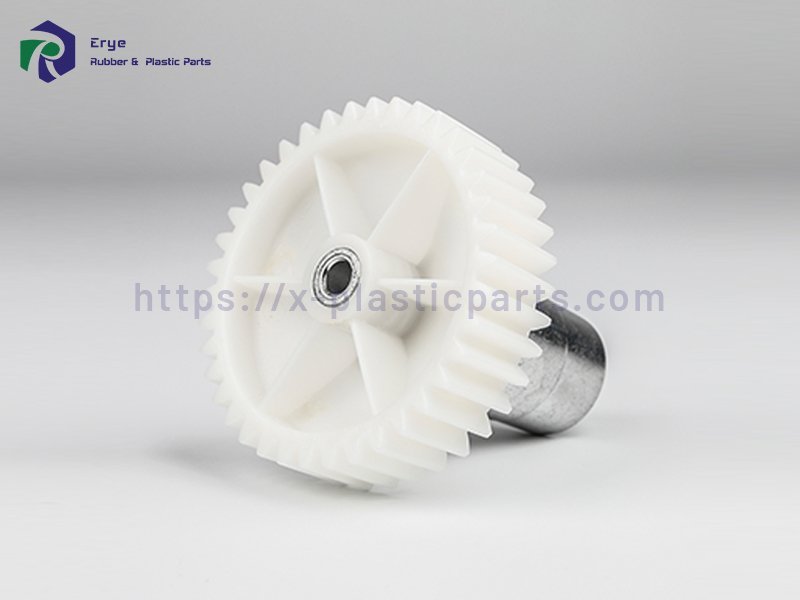
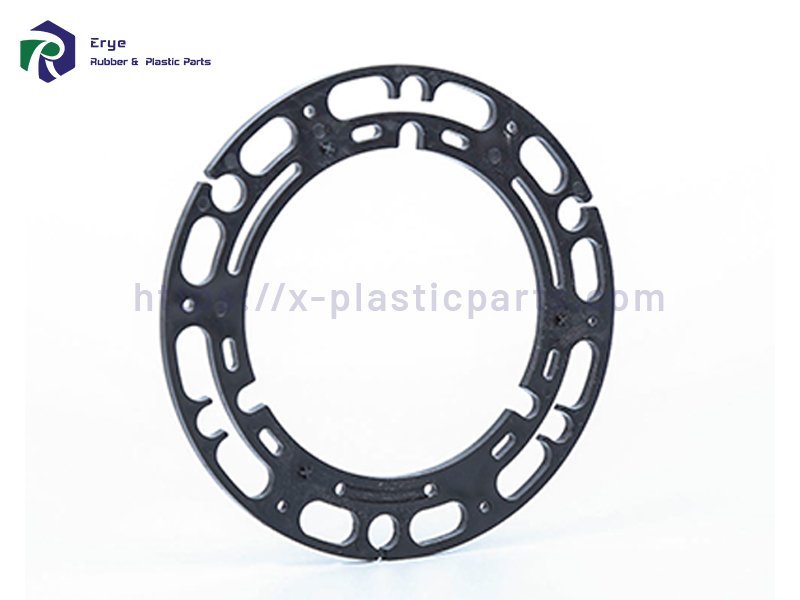