Overmolding Service
Overmolding(Overmolds, Over-molding) combines different materials, expanding design possibilities for parts that require unique dual material characteristics. It enhances product durability, grip, aesthetics, functionality.

What is Overmolds Service?
Overmolding is a manufacturing process that involves the injection of multiple materials to create a single, integrated component. It allows for the combination of a rigid plastic or metal substrate (the first material) with a softer, often elastomeric material (the second material) to form a single, cohesive part. This process enhances the functional and aesthetic properties of the final product and is commonly used in industries such as electronics, automotive, and consumer goods to improve grip, reduce vibration, or create multi-textured surfaces.

Overmolds Working Process
Designing for Over-molding
It is critical to ensure that your parts are properly designed for the overmolding process. The design process begins with understanding the function of the part. Answering these questions will help you determine which material is best suited for your purpose.
- What will the part be exposed to? – Exposure to the sun’s UV rays or harsh chemicals can damage certain types of plastics. If you know where the part is going and what it will be exposed to, you can choose a material that is more UV resistant than others.
- Why overmold parts? – If you’re using TPE material on a handle, it may be for grip, ergonomics, comfort, or shock absorption.
- How long is the production cycle time? – Component design factors affect cycle time and unit price. For example, shock absorption can be added to a product by increasing the thickness of the TPE, which may result in a longer cycle time.
How does overmolding work?
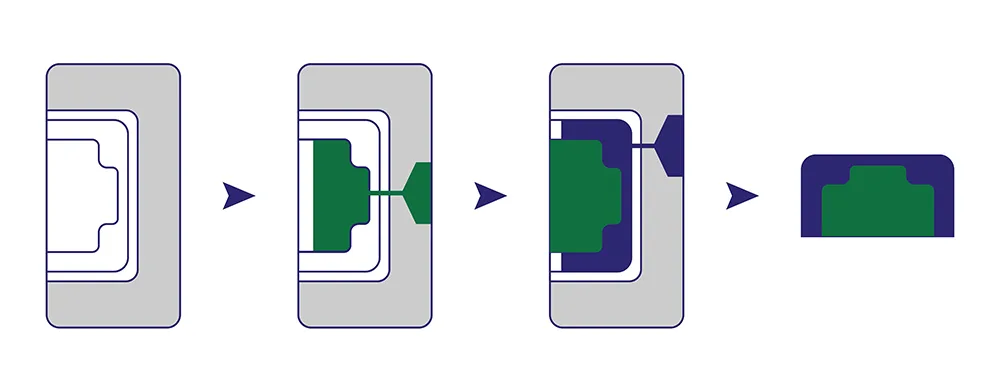
Overmolds is a multi-stage process that seamlessly combines different materials to create intricate and efficient parts. The overmoulding process involves several key steps:
- Injecting the Base Material: The first step involves injecting the primary material into the mold cavity, forming the base of the part.
- Applying the Overmold: In this stage, a second material, known as the overmold, is injected over the base material. It bonds seamlessly to create a composite part.
- Cooling and Solidifying: After the overmolding, the combined materials are allowed to cool and solidify within the mold, ensuring a secure and durable bond.
- Ejecting the Finished Part: Once the part has fully solidified, it is ejected from the mold, revealing the completed overmolded component.
Custom Plastic Parts
Custom Rubber Parts
Custom PU Parts
Materials for Overmolding Parts
Factors to Consider Before Selecting Materials
When selecting a material, both the base material and the overmolding material should be considered.TPE plastics come in many variations depending on their physical properties and their ability to adhere to other plastics.
- Bonding – Some materials with chemical bonding will be overmolded with and without adhesion due to compatibility issues between the two. If the materials don’t bond together or don’t need to be bonded together, mechanical bonding such as undercuts and indentations can be designed to ensure a lasting connection.
- Temperature – Substrates must not deform under the heat and pressure of the injection molding process.
- Tensile – Related Properties – Tensile strength, elongation, tensile modulus, and several other related properties can better address how a product will behave under tensile conditions.
- Compression Properties – Since TPE plastics are most commonly used for their flexibility, it is important to understand how far a part can be compressed without causing permanent damage.
- Coefficient of Friction – Friction is the force required to move one surface to another, such as the surface texture of a mold.
- Hardness – The hardness property is the ability of a material to resist indentation. Different pressures are used because the hardness of different materials can vary greatly.
- Flexural Modulus – The resistance of a material to bending is the flexural modulus and should be taken into account for gripping characteristics.
- Material Thickness – The thickness of a material will change the effectiveness of the material’s properties. thicker walls of a TPE will absorb more vibration and feel softer.
Related Resources
Our Available Material
Overmolds Material Compatibility Chart
There are two main types of layer bonding. One is actual chemical bonding at the interface of the two resin layers; the other is mechanical bonding, which depends on the physical geometry at the interface. Acceptable bonding is achieved through a combination of part design, material selection, mold design and molding process. Demonstrate a set of professional and reliable material selection parameters:
M = mechanical bond C = chemical bond
Overmold Material | ABS | ABS/PC | PC | PBT | PP | PA |
---|---|---|---|---|---|---|
TPU | C | C | C | C | M | M |
TPV | M | M | M | M | C | M |
TPE | M | M | M | M | C | M |
LSR | - | - | M | M | - | M |
TPC | C | C | C | C | M | M |
TPE | C | C | C | M | M | M |
TPE | M | M | M | M | M | C |
TPE | M | M | M | M | M | C |
TPE | M | M | M | M | M | C |
TPE | C | C | C | M | M | M |
LET’S START A NEW INJECTION MOLDED PARTS
Waht is the Advantages of Overmolding Services?
Enhanced Product Durability
Overmolding adds an extra layer of protection, improving resistance to wear, impact, and environmental factors.
Improved Ergonomics and Aesthetics
It allows for the integration of soft-touch grips and colorful designs, enhancing user comfort and product appeal.
Reduced Assembly and Labor Costs
By combining multiple components into one, overmolding reduces the need for assembly and lowers labor costs.
Seamless Bonding of Dissimilar Materials
Overmolding enables the secure bonding of different materials, offering a wider range of design options.
Downside of Overmolding
Material Compatibility Concerns
Ensuring compatibility between the base and overmolded materials can be a challenge, as selecting an incompatible combination can lead to issues.
Extended Production Times
Overmolding processes may be slower than traditional molding methods, affecting production timelines.
Material Waste Generation
Overmolding can generate material waste as not all of the overmolded material may be used efficiently.
Increased Production Costs
Additional materials and processes in overmoulding can elevate production costs compared to traditional molding methods.
Limited Material Choices
Overmolding may restrict material options for specific applications, as not all materials are suitable.
Compare | Insert Molding | Overmolding |
---|---|---|
Process | Inserts places in mold, mateiral injected around them | Second material injected to encase preformed part |
Material Combination | Combines different materials with a part | Adds an outer layer to an existing part |
Applications | Embedding components, combing materials | Enhancing aesthetics, functionality, for ergonaomics |
Cost | Cost-effective for material combination | Cost-effective for adding outer layer or features |
Overmoulding Products We Made
Warning: Attempt to read property "post_type" on null in /home/u811379278/domains/x-plasticparts.com/public_html/wp-content/plugins/elementor/includes/utils.php on line 927
Warning: Attempt to read property "post_status" on null in /home/u811379278/domains/x-plasticparts.com/public_html/wp-content/plugins/elementor/includes/utils.php on line 933
Warning: Attempt to read property "post_status" on null in /home/u811379278/domains/x-plasticparts.com/public_html/wp-content/plugins/elementor/includes/utils.php on line 936
Warning: Attempt to read property "ID" on null in /home/u811379278/domains/x-plasticparts.com/public_html/wp-content/plugins/elementor/includes/utils.php on line 937
Warning: Attempt to read property "ID" on null in /home/u811379278/domains/x-plasticparts.com/public_html/wp-content/plugins/elementor/includes/utils.php on line 939







Related Resources
Discover valuable resources covering multi-material molding processes, injection molding innovations, and precision molding techniques. Our expert content offers practical guidance on custom molding design, material selection, and manufacturing best practices to help you optimize your production and improve part performance.