Plastic Molding Material

Customized Plastic Molding Solutions
Additives to Improve Plastic Materials Property
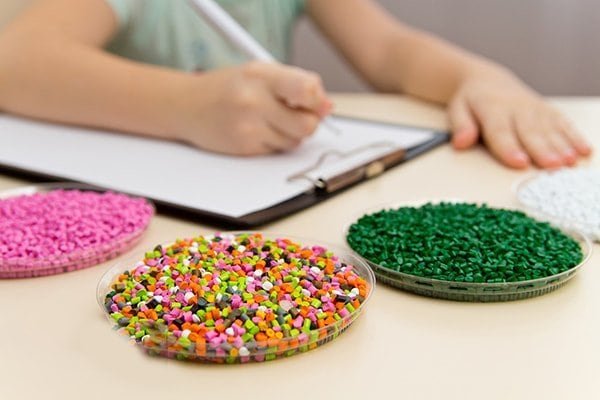
Common Plastic Molding Materials Options
Material selection is an integral part of the injection molding process. It affects the performance, cost and production time of your project. Conventional plastic materials:

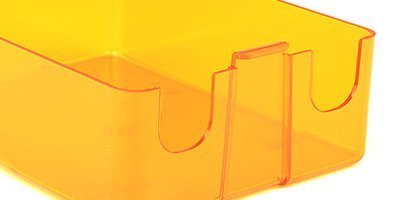







Choose the Right Plastic Material for Your Custom Plastic Parts
Key considerations for your custom plastic parts. Here are some tips to help you select the ideal plastic material for your specific needs, assisting you in making informed decisions for superior custom plastic products.
1. Consider Application Requirements
- Assess environmental factors like temperature and chemical exposure.
- Determine load-bearing capacity.
- Ensure the plastic can withstand the application’s specific conditions.
2. Evaluate Material Properties
- Focus on characteristics such as flexibility, strength, and electrical conductivity.
- Match material properties to your project’s performance needs.
3. Balance Cost with Performance
- Weigh material costs against performance requirements.
- Choose a material that meets your budget while delivering the needed performance.
4. Check Machinability
- Evaluate how easy it is to work with the material during manufacturing.
- Consider the complexity of your custom parts and choose a material that can be efficiently machined.
5. Determine Longevity
- Assess the expected service life of your custom parts.
- Consider wear and tear factors to select a material that provides durability over time.
LET’S START A NEW CUSTOM PLASTIC PARTS
What are Thermoplastics?
Thermoplastics are plastics that melt when heated and are known for their versatility and recyclability, making plastic injection molding possible. Because of this material’s versatility, robustness, flexibility, transparency and opacity, it is this versatility that makes thermoplastics such an attractive material for manufacturers.
Amorphous vs Semicrystalline Thermoplastics
Characteristic | Amorphous | Semicrystalline |
---|---|---|
Structure | Random arrangement | Partially ordered |
Physical Properties | Lower melting point, good impact toughness | Higher melting point, high strength |
Processing Characteristics | Easy to mold | More challenging to proces |
Applications | Optical and electronic products | Automotive, medical device |
Included Materials | PS (Polystyrene), PMMA (Polymethyl Methacrylate), PVC (Polyvinyl Chloride) | PE (Polyethylene), PP (Polypropylene), PBT (Polybutylene Terephthalate |
Properties and Uses of Common Plastic Materials
Nylon (PA)
PA properties:
- Low friction – does not heat up under high friction
- Chemical resistance – resistant to chemicals
- Abrasion resistant – suitable for elastomers and apparel applications
- Adaptable – can be combined with many other types of plastic materials
Nylon injection molding applications include:
- Rugged mechanical parts such as bearings, bushings, gears and slides
- Housings and snap-on closures
- Threaded inserts and power components
- Clamps and fixtures
Polycarbonate (PC)
Polycarbonate properties:
- Impact resistant – won’t scratch or dent under impact
- UV resistant – will not corrode or discolor under UV light
- Transparency – can be made into windows and eyeglass lenses
- Chemical resistance – will not corrode with chemicals
- Rigidity – suitable for eyeglasses and windows
Polycarbonate injection molding applications include:
- Mechanical guards
- Transparent and tinted windows
- Diffusers and light pipes for light emitting diodes (LEDs)
Polyoxymethylene (POM)
Polyoxymethylene properties:
- Rigidity – stays strong and doesn’t bend easily
- Impact Resistance – strong and stable enough to resist strong impacts
- Solvent Resistance – doesn’t corrode or rust due to chemicals and solvents
- Glossy surface – smooth, reflective properties
Polyoxymethylene injection molding applications include:
- bearings, gears, conveyor belts, pulley wheels
- fasteners,lock systems
- eyeglass frames
- parts for knives and firearms
Polypropylene (PP)
polypropylene properties:
- Chemical resistance – does not react with most bases and acids
- Fatigue resistance – retains its shape after repeated bending and flexing
- Electrical resistance – excellent insulating properties
- Elasticity – can be bent, flexed and deformed without actually breaking
Polypropylene injection molding applications include:
- Toys
- Storage containers
- Sporting goods
- Packaging
- Electrical appliances
- Power tool bodies
Acrylonitrile Butadiene Styrene (ABS)
ABS properties:
- Impact resistance – rubberized formulations make ABS impact resistant
- Surface hardness – some formulations have high stiffness
- Chemical resistance – unaffected by alkalis, water and most inorganic acids
- Uniform shrinkage – good dimensional stability
- Wide temperature range – resistant to heat and will not break in the cold
- Processability – easy to mold after cooling
ABS injection molding application including:
- Keyboard keys
- Protective caps
- Electrical outlet wall plates
- Automotive parts such as wheel covers
- consumer products
- Sports equipment
- Industrial accessories
Plastic Material Comparison Chart
Material | Approximate Tensile Strength | Flexibility | Impact Strength | Electrical Insulation | Temperature Resistance | Chemical Resistance | FDA Compliant | Cost (low to high) | Water Resistant |
---|---|---|---|---|---|---|---|---|---|
ABS | 5900 psi | high | high | no | low | medium | no | medium | yes |
PA | 12400 psi | high | high | yes | high | strong | yes | high | yes |
PC | 9500 psi | high | high | no | high | weak | yes | high | yes |
PE | 3480–6530 psi (HDPE) 800–13100 psi (PET) 1400 psi (LDPE) | medium (LDPE) low (HDPE) high (PET) | high (LDPE) high (HDPE) low (PET) | yes | low | strong (LDPE) strong (HDPE) strong (PET) | yes | low | yes |
POM | 6400–10600 psi | medium | high | yes | high | strong | yes | high | yes |
PP | 4800 psi | high | medium | yes | medium | strong | yes | low | yes |
PS | 2560–7690 psi | medium | high | no | low | medium | yes | low | yes |
PVC | 7500-8000 psi | medium | high | yes | low | medium | yes | medium | yes |