Thermoplastic Elastomer Molding Material
Thermoplastic elastomers (TPEs) are one of the most versatile plastics on the market due to their design and manufacturing flexibility. They combine the processing advantages of thermoplastics with the performance characteristics of elastomer. Therefore, it is relatively easy to process TPEs using thermoplastic methods such as extrusion, over-molding and injection molding.
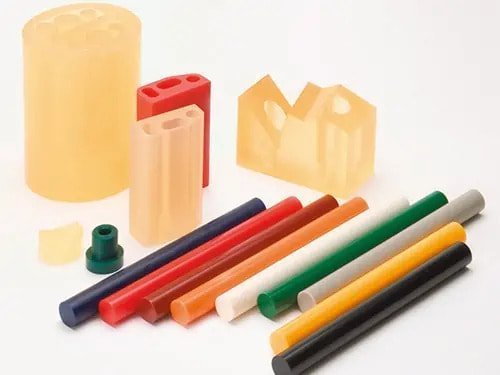
Customized TPE Material Solutions
TPE Molding Grade Regulatory

Thermoplastic-Elastomer Molding Material Options
There are many types of TPE molding, these are just a few more examples, each with its own unique set of properties that make them suitable for specific applications.Within the TPE product portfolio, several materials provide excellent bonding performance to other substrates, including PE, PP, ABS, PC/ABS, Co-Polyester, Nylon and Propionate.



Choose the Right TPE Material for Your Custom Parts
Key considerations for your TPE molding material custom parts. Here are some tips to help you select the ideal material for your specific needs, assisting you in making informed decisions for superior custom TPE molded products.
1. Consider Application Requirements
- Assess environmental factors like temperature and chemical exposure.
- Determine load-bearing capacity.
- Ensure the plastic can withstand the application’s specific conditions.
2. Evaluate Material Properties
- Focus on characteristics such as flexibility, strength, and electrical conductivity.
- Match material properties to your project’s performance needs.
3. Balance Cost with Performance
- Weigh material costs against performance requirements.
- Choose a material that meets your budget while delivering the needed performance.
4. Check Machinability
- Evaluate how easy it is to work with the material during manufacturing.
- Consider the complexity of your custom parts and choose a material that can be efficiently machined.
5. Determine Longevity
- Assess the expected service life of your custom parts.
- Consider wear and tear factors to select a material that provides durability over time.
LET’S START A NEW CUSTOM TPE MOLDING PARTS
What Is a Polymer?
Polymers are large molecules composed of repeating small and simple chemical units. Based on their ability to form, they can be categorized as follows.
- Thermosets: Polymers characterized as insoluble and unable to melt. They owe their strength to reactive oligomers or resins that react with cross-linking agents under heat and pressure to form cross-linked networks. Polyurethanes and epoxy resins are common thermoset plastics.
- Thermoplastics: Polymers characterized by ease of melting and molding. They melt with heat and harden on cooling. Common materials are nylon, polyester and polyolefins.
- Elastomers: Characterized by elastic natural or synthetic polymers that can be elastically deformed under tensile and compressive stresses, but then return to their original shape. Common ones are natural rubber and silicone rubber.
- Thermoplastic elastomers: TPEs combine the properties of thermoplastics and elastomers: they are materials that are processed like plastics but have the excellent performance characteristics of rubber. Examples are TPU and TPV.
Properties and Uses of Thermoplastic Elastomer
TPU (Thermoplastic Polyurethane)
Thermoplastic Polyurethane Properties:
- Elasticity: TPU exhibits excellent elasticity and flexibility, maintaining performance across a wide temperature range.
- Abrasion Resistance: It possesses high abrasion resistance, making it suitable for applications with significant wear.
- Chemical Resistance: TPU demonstrates good resistance to oils, fats, and various chemicals.
- Processability: It can be processed using methods such as injection molding, extrusion, and blow molding.
- Transparency: TPU can be manufactured in a transparent form, suitable for applications requiring visual appeal.
- Low-Temperature Performance: Maintains good elasticity even in low-temperature environments.
TPU injection molding material Applications:
- Footwear: Used in soles and cushioning materials for athletic shoes.
- Electronics: Employed in mobile phone cases, protective covers, and other electronic device components.
- Industrial: Utilized in conveyor belts, seals, hoses, and tires.
- Medical: Commonly used in medical devices and packaging materials.
- Consumer Products: Found in household items, toys, and sports equipment.
TPV (Thermoplastic Vulcanizate)
Thermoplastic Vulcanizate Properties:
- Elasticity: TPV provides rubber-like elasticity, enabling it to return to its original shape after deformation.
- Weather Resistance: Exhibits good resistance to UV radiation and environmental aging, making it suitable for outdoor applications.
- Chemical Resistance: It offers reliable resistance to a variety of chemicals.
- Processability: Can be processed and reshaped like thermoplastic materials.
- High Strength: Typically possesses higher strength and rigidity compared to TPU.
TPV injection molding material Applications:
- Automotive Industry: Used in automotive seals, vibration dampers, and interior/exterior components.
- Building Materials: Applied in roofing membranes, window frame seals, and other construction applications.
- Appliances: Utilized in the housings and seals of household appliances.
- Industrial: Employed in tubing, flexible connectors, and insulation materials.
TPE Molding Material Comparison Chart
TPE Type | Approximate Tensile Strength | Flexibility | Impact Strength | Electrical Insulation | Temperature Resistance | Chemical Resistance | FDA Compliant | Cost (low to high) | Water Resistant |
---|---|---|---|---|---|---|---|---|---|
TPE | 290 – 8200 psi | high | high | no | low | strong | no | high | yes |
TPU | 4060 – 13900 psi | high | high | no | high | strong | yes | medium | yes |
TPV | 1,450 - 4,350 psi | high | high | yes | medium | medium | yes | medium | yes |